High frequency press combines capacity with flexibility
Successful collaboration: Erland Lundby, Managing Director at Termowood (left) and Bruno Kallesøe
Do you want to know more about our Mulitply C press line?
Multi-layer solid wood panels
At Norwegian company Termowood Kallesoe Machinery has installed a high-frequency press line for production of multi-layer panels.
With the Tewo system, Norwegian company Termowood has developed a construction system that looks just like conventional cross-laminated timber on the outside. In reality, however, the 20 cm narrow bar elements consist of two three-layer boards insulated in the middle. As a rule, they are 40 mm thick panels filled with insulation materials such as wood fiber or mineral wool. With this system, the company produces complete construction sets of wall or ceiling components where the single elements maximally weigh 25 kg, meaning that they can be installed by one person alone. Managing director Erland Lundby highlights the high degree of pre-fabrication of the tailormade, insulated system components as one of the main advantages of the patented systems.
Successful development
Due to brisk demand, Termowood invested in a new production line for constructing the elements in 2019, and the launch of a three-layer panel line followed in 2020. For panel production, Termowood relies on a Multiply C high-frequency press solution from Kallesoe Machinery. „We looked at a number of solutions, and finally decided on Kallesoe,“ Lundby reports, highlighting the short pressing times and the high flexibility as decisive factors in the purchasing process.
Flexible and powerful
Kallesoe specially designed the system for up to 60 mm thick multi-layer boards that are glued crosswise. In addition to the fully automated HF press, Kallesoe also supplied the lay-up unit complete with feeding system. There, the longitudinal lamellae are glued at the edges and gathered as layers in accordance with the desired panel dimensions. A vacuum feeder lifts them onto the lay-up table where a movable surface application device takes care of applying the adhesive. Then, the vacuum lifter adds the cross layer, and after another round of gluing, the final longitudinal layer is put on top.
In the following step, the press batch is brought into the HF system which applies lateral and top pressure as needed. With the help of high-frequency energy, the glued joint is heated which causes it to harden quickly and completely. The system allows for the production of panels with different lengths; short products are arranged in several rows in the press. „This way, we fully utilize the capacity of the press and the products can be customized according to the order,“ CSO Bruno Kallesøe reports and adds that the Multiply C system is the perfect way to optimally combine performance with flexibility.
After the press line, Kallesoe implemented two circular saws. The first one trims the panels before the second multi-blade saw separates them into longitudinal stripes which is the final form for the Tewo elements. Furthermore, Kallesoe Machinery installed a planing and sanding system which is used to finish visible surfaces.
All according to plan
Only a few months after commissioning, Lundby is extremely satisfied: „Kallesoe delivered exactly what we had agreed on. And even though delivery took place right during the peak of the Corona crisis, there were no delays on the part of the Danes. In close collaboration we were able to master all challenges in a short time and launch the plant as planned.“ With the new systems, Termowood‘s production capacity reached one housing unit per shift.
Source: CLT Special 2020
Check out the video of the press line below.
References
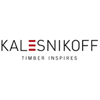
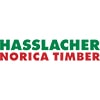
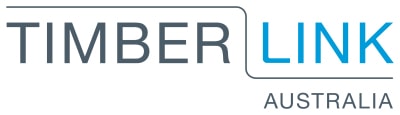
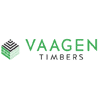
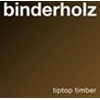
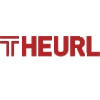
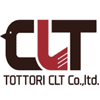
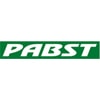
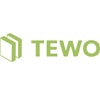
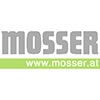
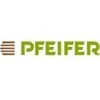
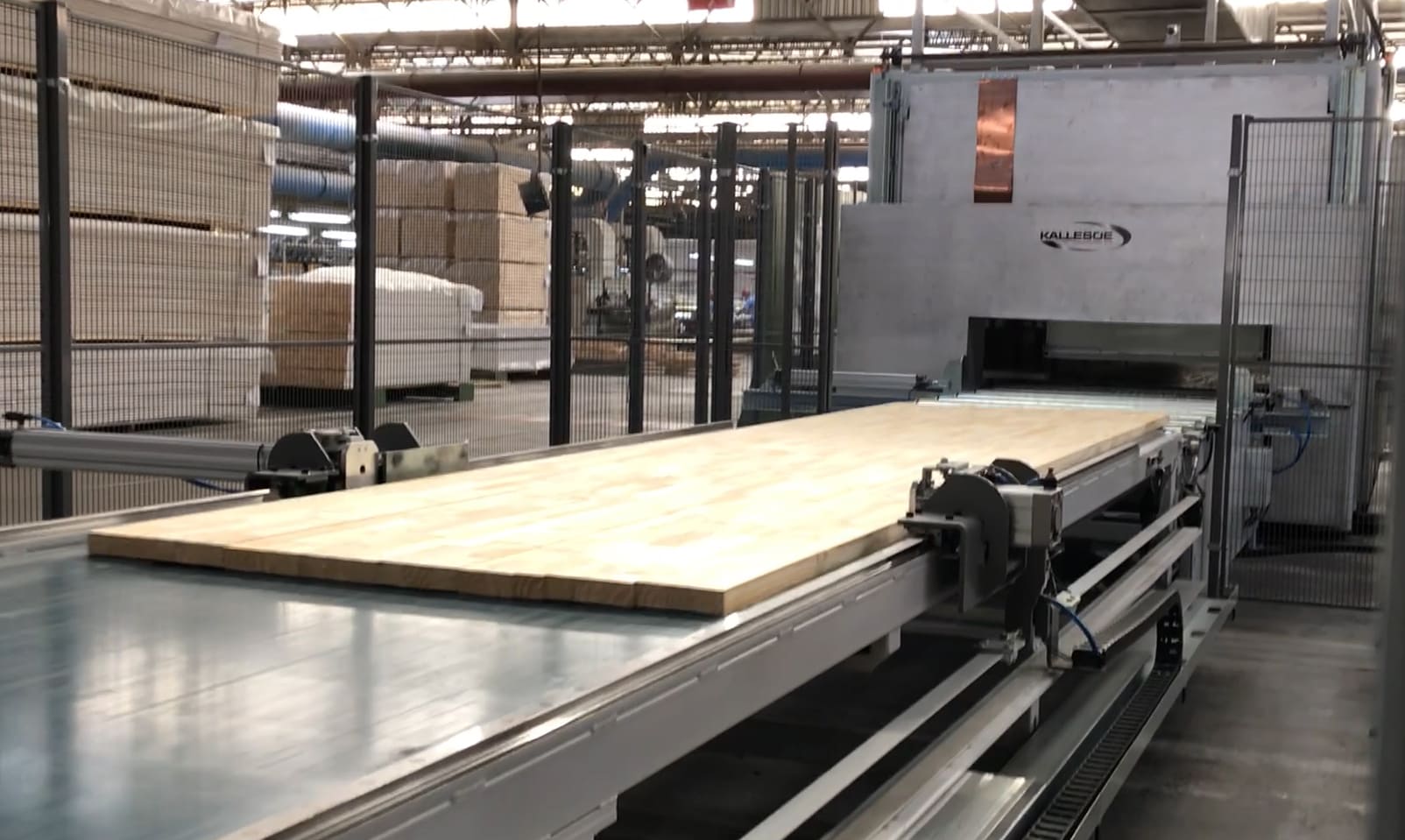
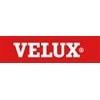
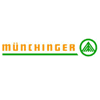
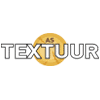
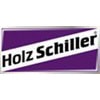
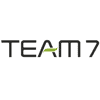
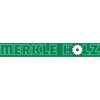
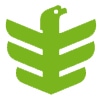
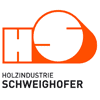
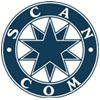
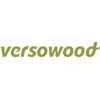
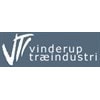
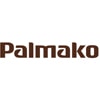
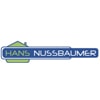
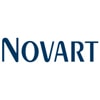

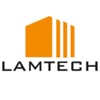
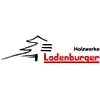
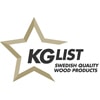
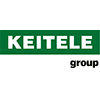
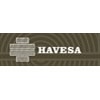
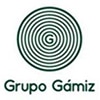
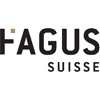
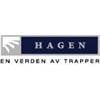
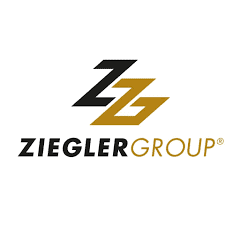
“We have been in this business for 82 years. Kallesoe is by far the best and most professional supplier we have ever done business with. They are so easy to work with, and they know their products and business area. It has been a pleasure. It is important to go the extra mile to make sure that the customer is satisfied – and they do that at Kallesoe.”
„Kallesoe were the only plant suppliers who kept what they had promised. Set up, turn on, produce“
“Once again it was a successful collaboration with Kallesoe – everything went according to plan”