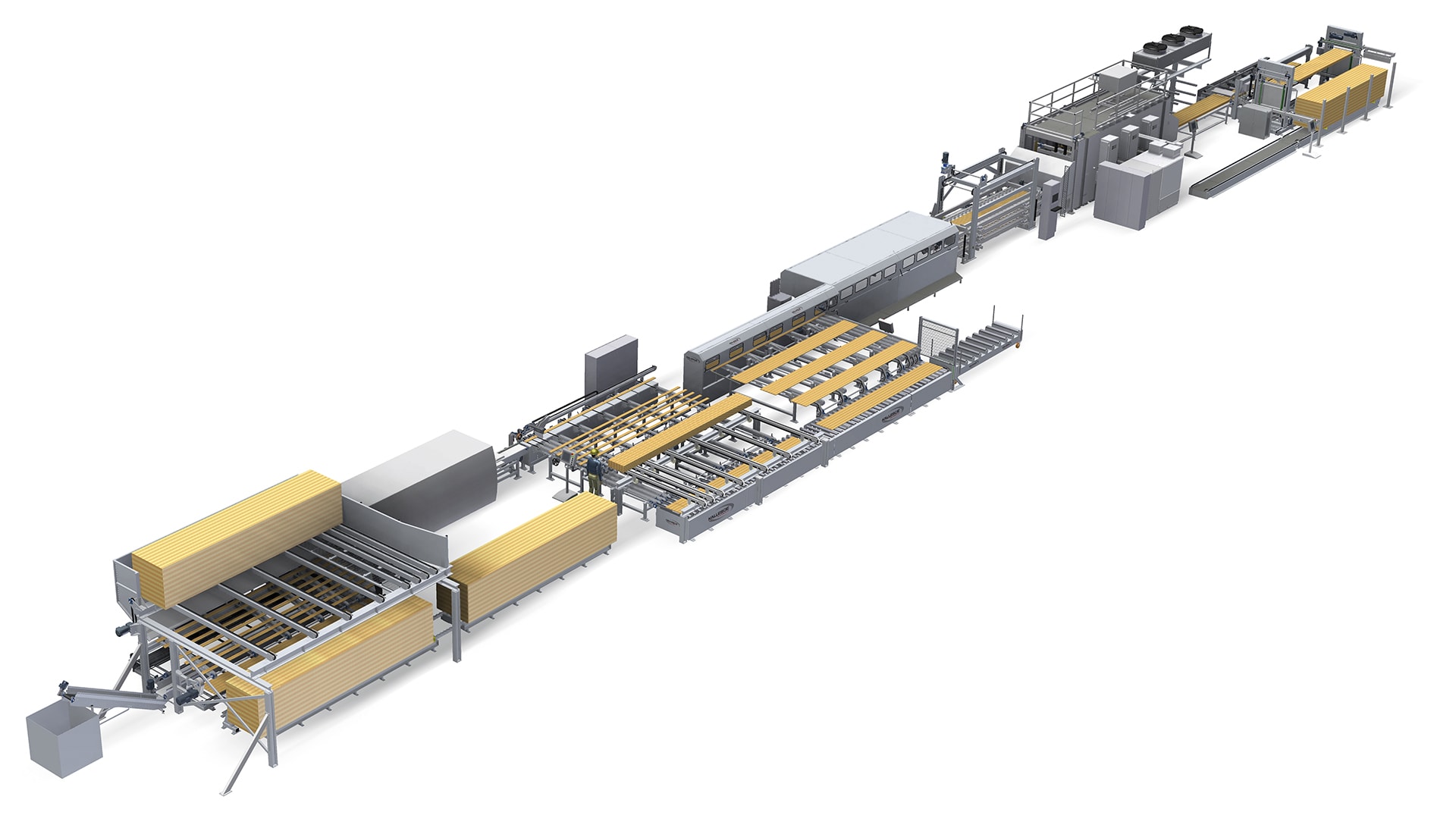
Solutions for high capacity production of scantlings, posts, and beams
We are dedicated to find the right set-up for your production of scantlings, posts, and beams. Based on your specific needs we put together exactly the right system solution for you and your business. We have decades of experience in delivering system solutions that guarantees the highest capacity in the best quality.
With our flexible machine solutions and the latest technology, we can tailor a system solution that optimizes your production.
You know the need, together we find the solution.
Inspiration
Your solution is designed uniquely for you
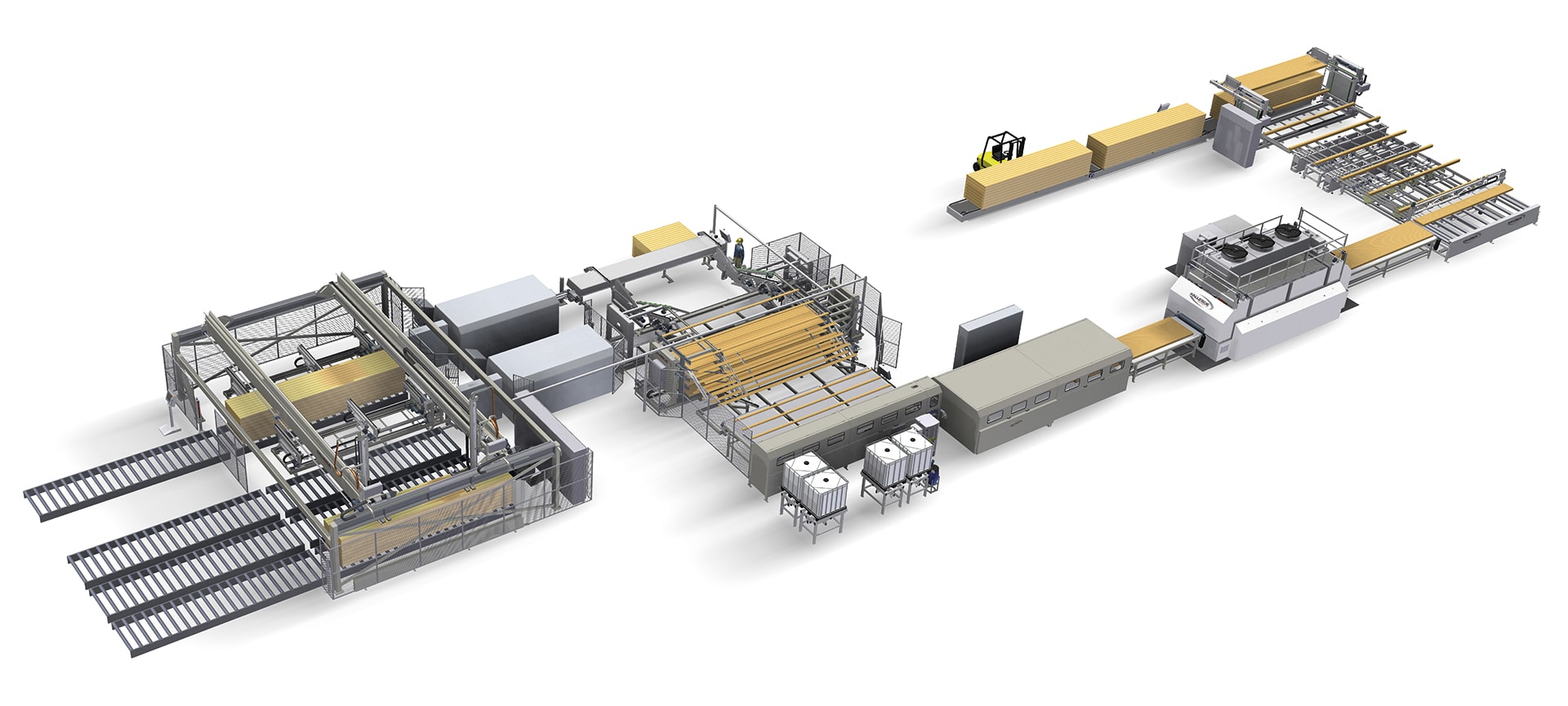
Frame wood solution
System solution for window components.
This system solution shows a complete manufacturing line for window components which allows for the use of three different kinds of wood quality. The infeed lamella stacks are handled by a vacuum gantry serving two planers after which the lamellas are transported to a sorting system.
The lamellas are distributed in the right order in accordance with a preset program before entering the gluing system.
The lamellas are face glued before they reach the layup where they are turned 90º and gathered in a batch on the press infeed belt in front of the RF press. The glue between the different components is left out. The full batch is moved into the RF press where it is pressed. The finished products are cross conveyed, separated, and stacked, ready for pick-up.
Optionally the finished products can be cut to length.
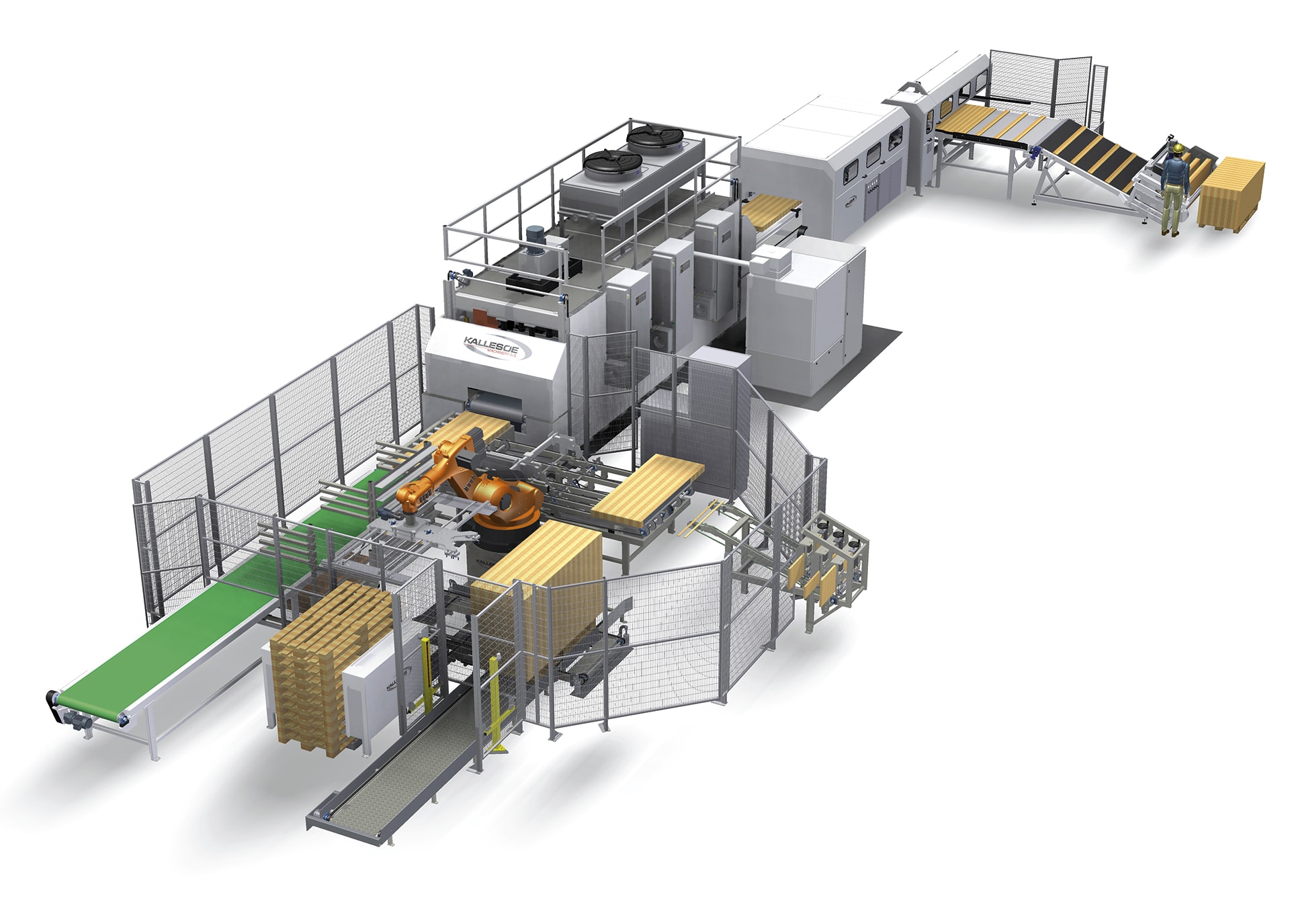
System solution for scantlings
With a robot (de)stacker solution.
This system solution shows a window component line with a manual lamella infeed magazine that feeds the gluing system with the right combination of lamellas. Before they reach the layup, the lamellas are face glued and glue is left out between the different components. Here they are turned 90º and gathered to form a batch on the press infeed belt. The batch is moved into the RF press where it is pressed. After pressing the components are stacked onto pallets by an automated robot.
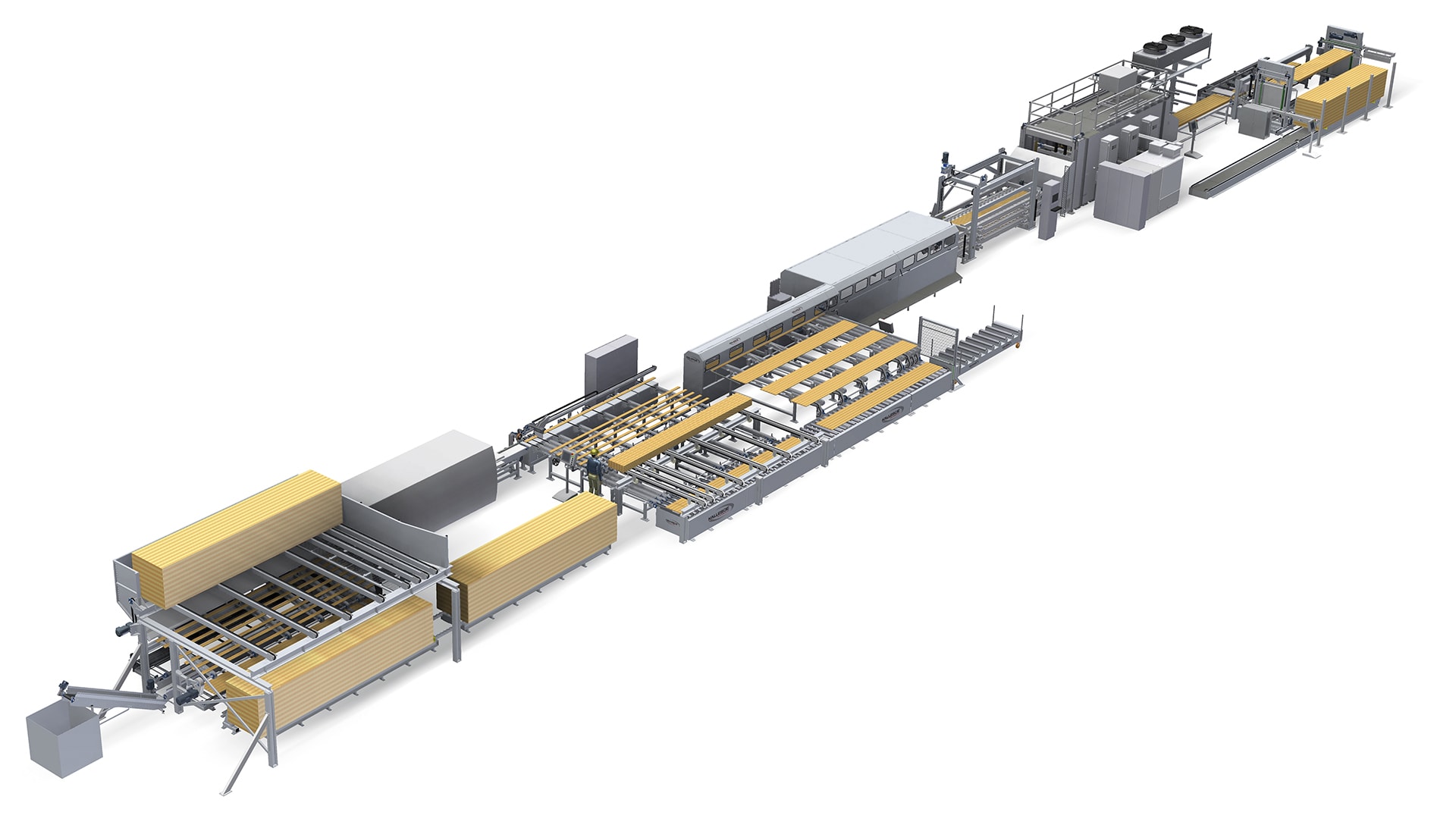
Press system for window components
Press solution with very short pressing times.
The radio frequency solution from Kallesoe Machinery is a reliable plant for the production of frame wood, profiles and duo and trio beams.
The lamstock stack is placed on the infeed system, which also allows for end cutting of the wood before the lamstock is transported through a planer one by one. The lamstock is sorted manually and defective lamellas are rejected.
The lamstock is then fed through the gluing and stacking system where the complete batch is formed.
If using hardwood, a multi-layer buffer station can be added before the batch is fed into the press. The batch can be parked inside the press to give the glue extra time to penetrate the wood.
The glue is cured in the radio frequency press, and the finished elements are transported to final stacking.
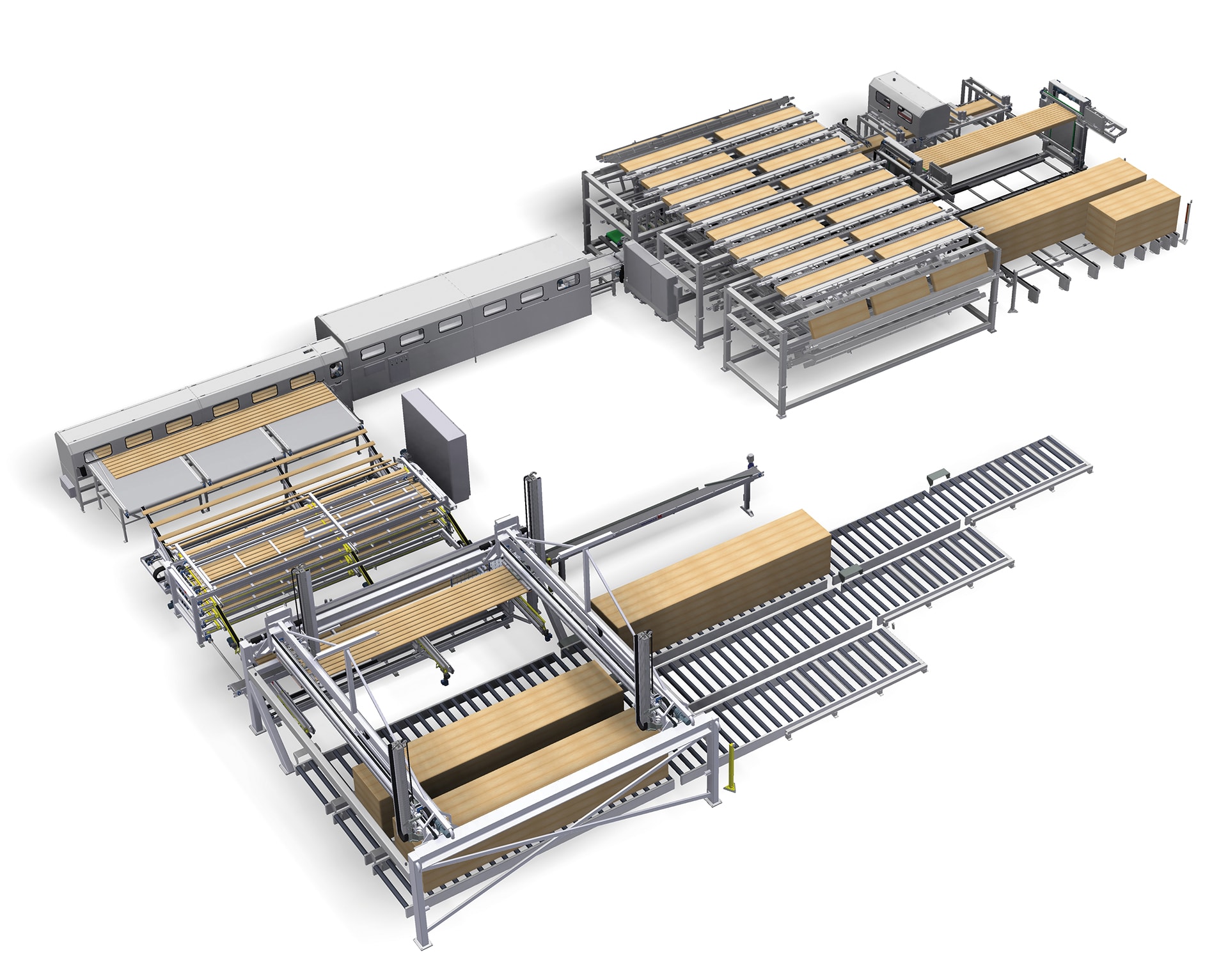
Press system for window components
With a cold setting press section.
This press system shows a cold setting press line for window components allowing for the use of three different wood qualities. A vacuum gantry feeds a sorting system with pieces from the lamella stacks. Before they enter the gluing system, the different lamellas are distributed in the right combination according to a preset program.
The lamellas are face glued before they reach the layup, where they are turned 90º and gathered to form a batch on the press infeed belt. Glue is left out between different components in the batch, so they can be pressed at the same time. The batch is moved to the sectional cold setting press.
According to capacity requirements, the press is designed with the needed number of press sections. The press is designed as an endless chain where the sections are moved around in one cycle and thereafter unloaded. The pressed products are cross conveyed and stacked. Optionally the finished products can be cut to length.
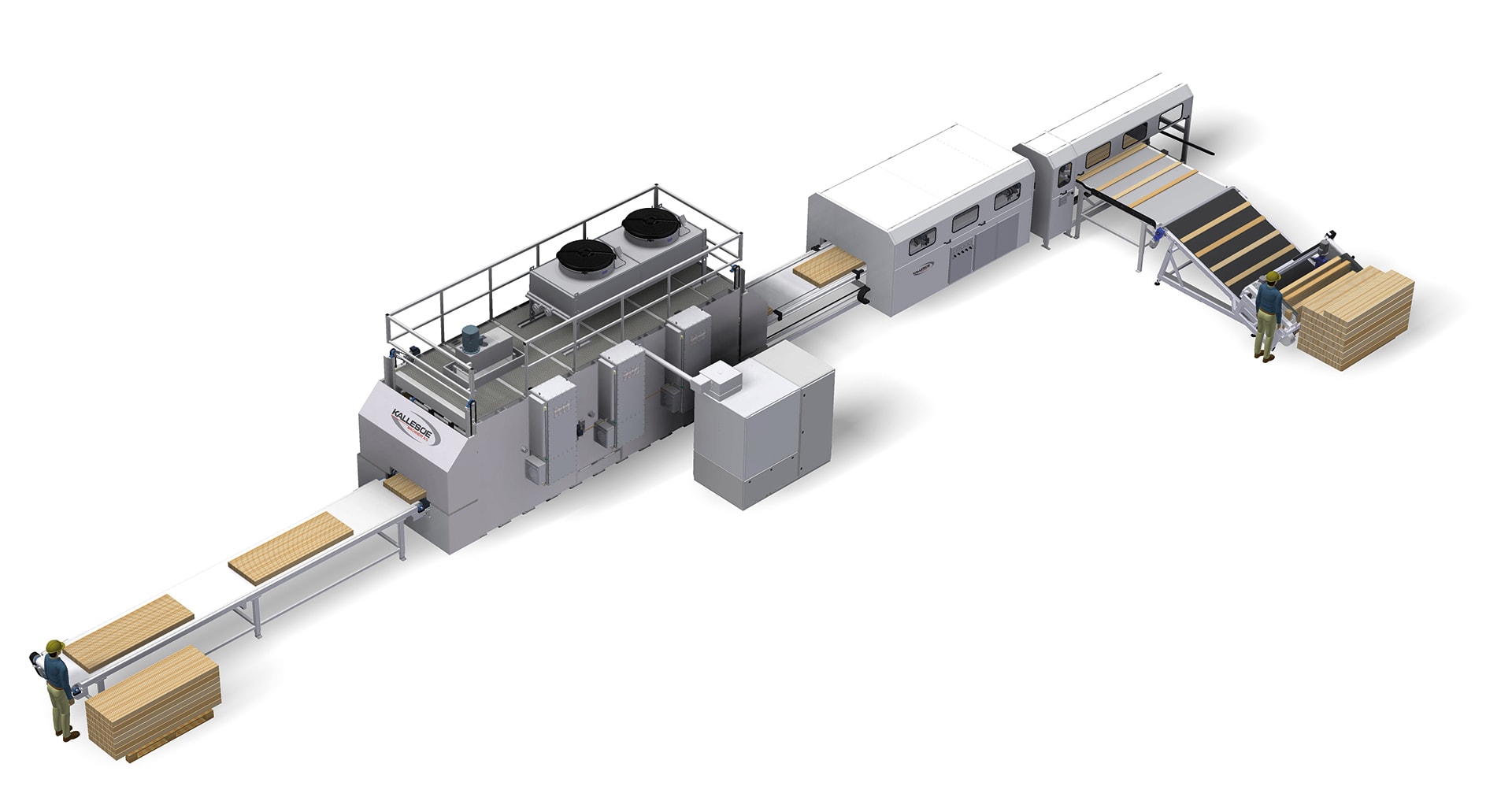
Press system for window components
With a manual infeed system.
This press system is an example of a basic system that manufactures window components. The system operates with a manual infeed and outlet system. The lamella magazine feeds the gluing system in the right combination. The lamellas are face glued before they reach the layup, where they are turned 90º and gathered to form a batch on the press infeed belt. Glue is left out between the different components in the batch, so they can be pressed at the same time. The batch is moved to the RF-press. After pressing the components are stacked manually. A small vacuum gantry can be added to ease this process.
”The collaboration with Kallesoe was really good. The machinery is performing to our full satisfaction.”
“The changeover possibilities of the press were crucial to us since we deliver to markets that demand different dimensions of the products.”
“The technology was very impressive. We are convinced that it is much better than other technologies on the market. It is all about flexibility and speed.”
References in the scantling, post, and beam industry
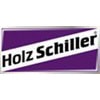
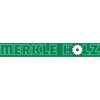
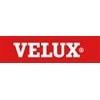
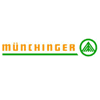
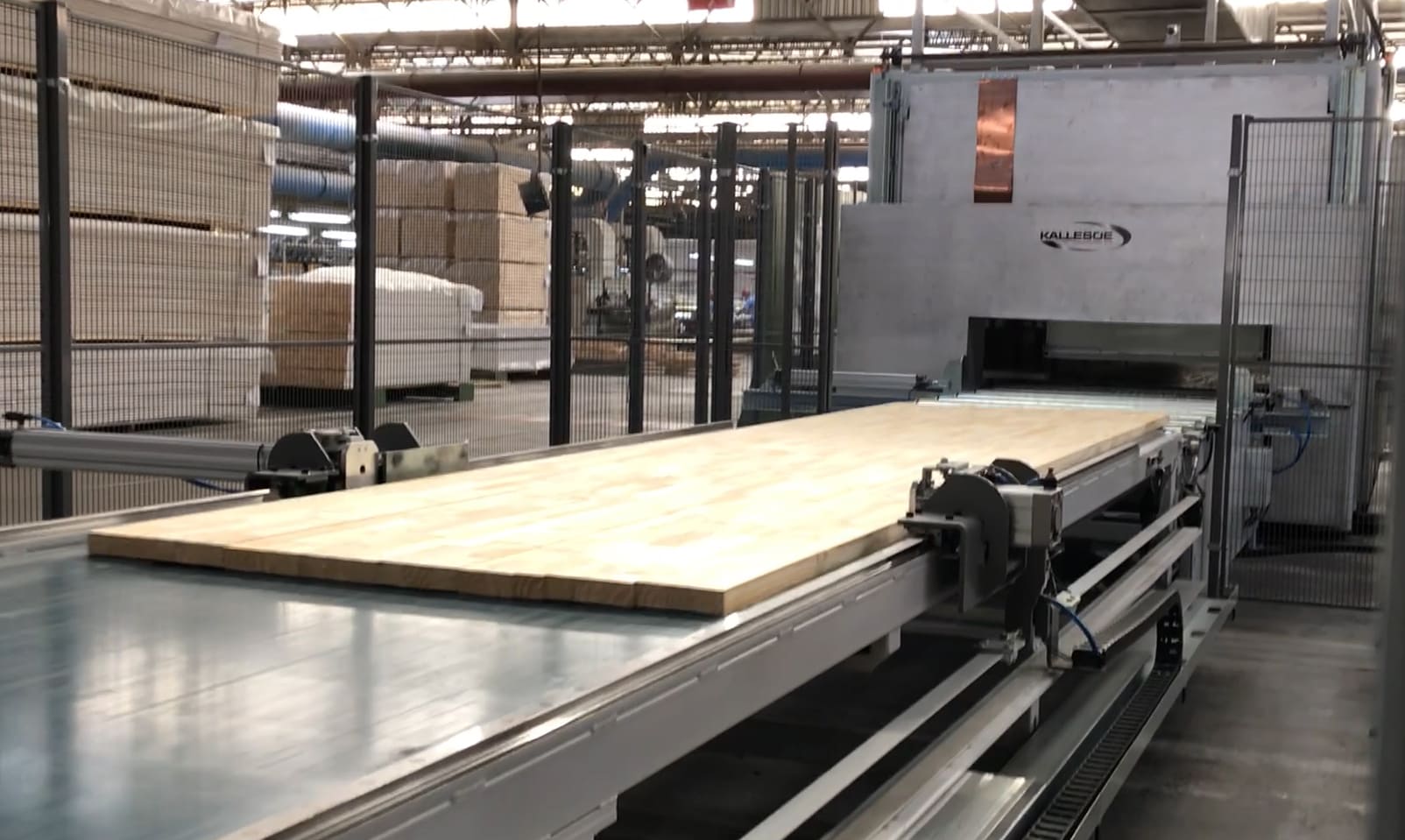
