Custom-made solutions for glulam production
It is crucial to us that we deliver exactly the right system solution for your glulam production. Our experienced staff are here to help you secure the right turn-key solutions for your business.
In close collaboration with you we can put together precisely the right system solutions to make sure you achieve the highest quality and capacity in your production.
If you are looking for the best solution for your glulam production, you will find it here with us.
Find examples of our glulam solutions here
Your solution is made uniquely for you
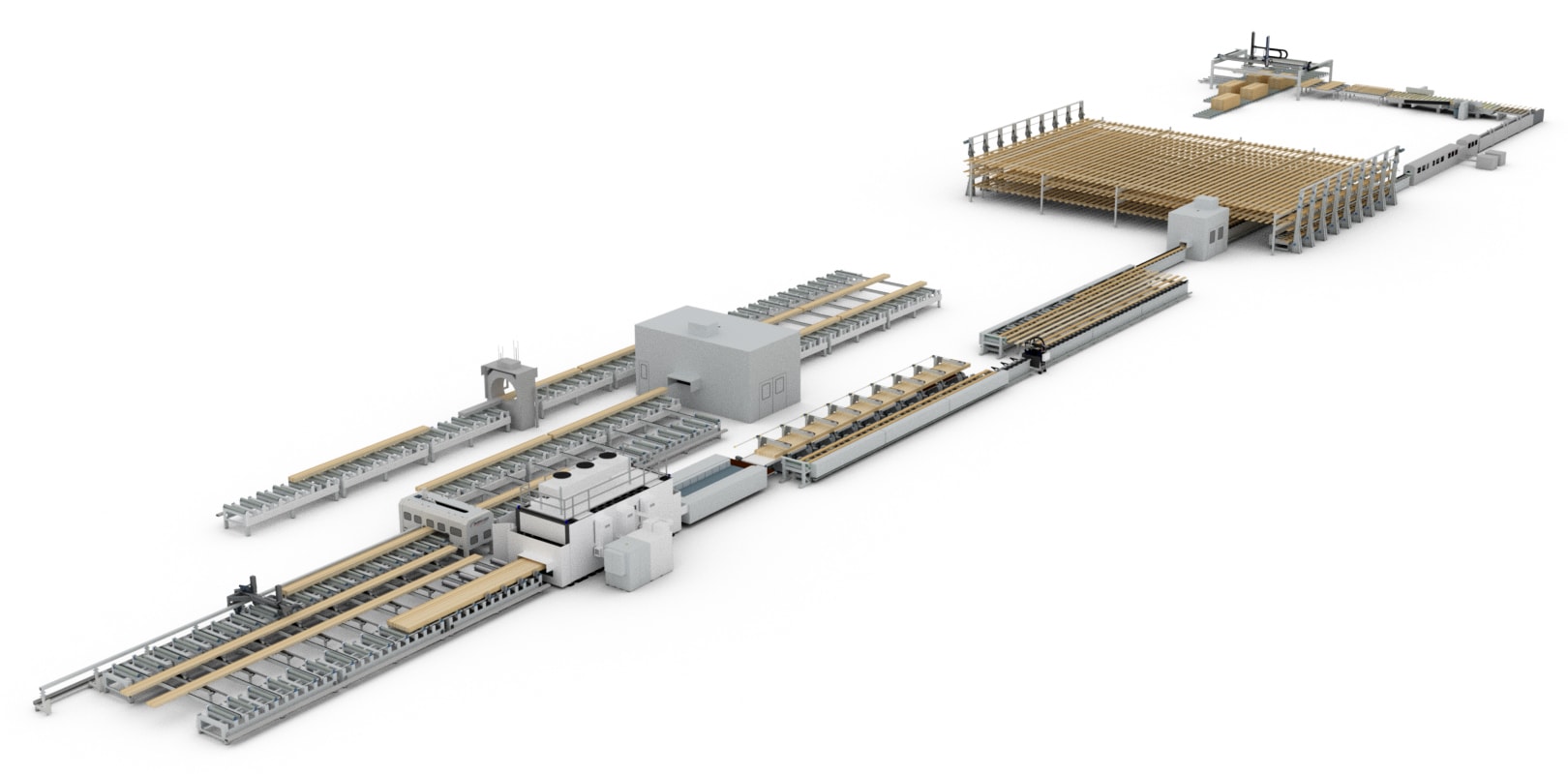
Fully equipped glulam system
With this solution you get a complete production line for glulam beams (GLT).
The lamstock is produced in a finger jointing machine independently of each other and with the desired lengths. The finished lamstock is led to a high storage for drying.
The high storage supplies the line with the correct number of lamstock that is needed for the glulam beam.
Glue is added individually to the lamstock with a face gluing unit, and they are joined in the lay-up system. When a batch is ready it is led into the high frequency press, where the beam is pressed in steps of 6 meters at a time. The task time depends on the dimensions of the glulam beam and the type of glue.
After pressing, the individual beams are separated and can be sawn to size. They are then passed through a planer and for further finishing.
One of the advantages of a beam production line with Kallesoe’s radio frequency press is that beams of different lengths can be produced in the same batch – this provides great flexibility.
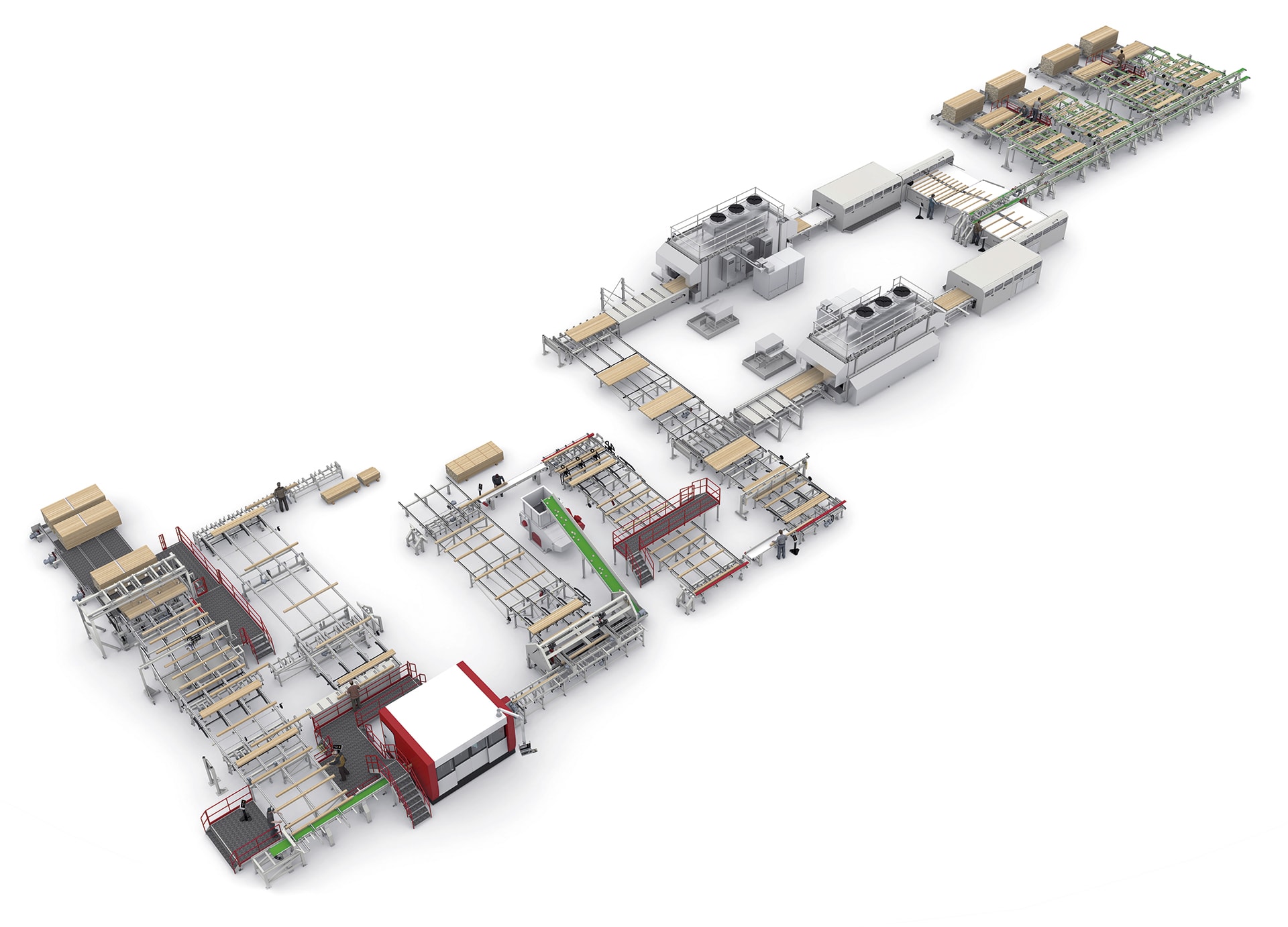
Double press system for small beams and posts
The system can be provided with one or two press lines, as required.
The plant offers a very efficient production and is designed for laminating products of up to max. 6 meters in length, typically smaller glulam beams and window components.
The lamstock, which can be in several qualities, is fed to the gluing and lay-up system in a predetermined order. They are face glued, tilted up 90º and assembled into a batch. The lay-up table is filled with one or more lengths (rows), after which the batch is led into the radio frequency press for quick curing of the glue.
After pressing, the items are led on for separation, shortening, planing, possible sorting and quality control. Finally, they are stacked for packing.
Glulam and CLT facility
Our most advanced system that offers you a compact flexible production line for glulam and CLT in one; from wood to engineered products.
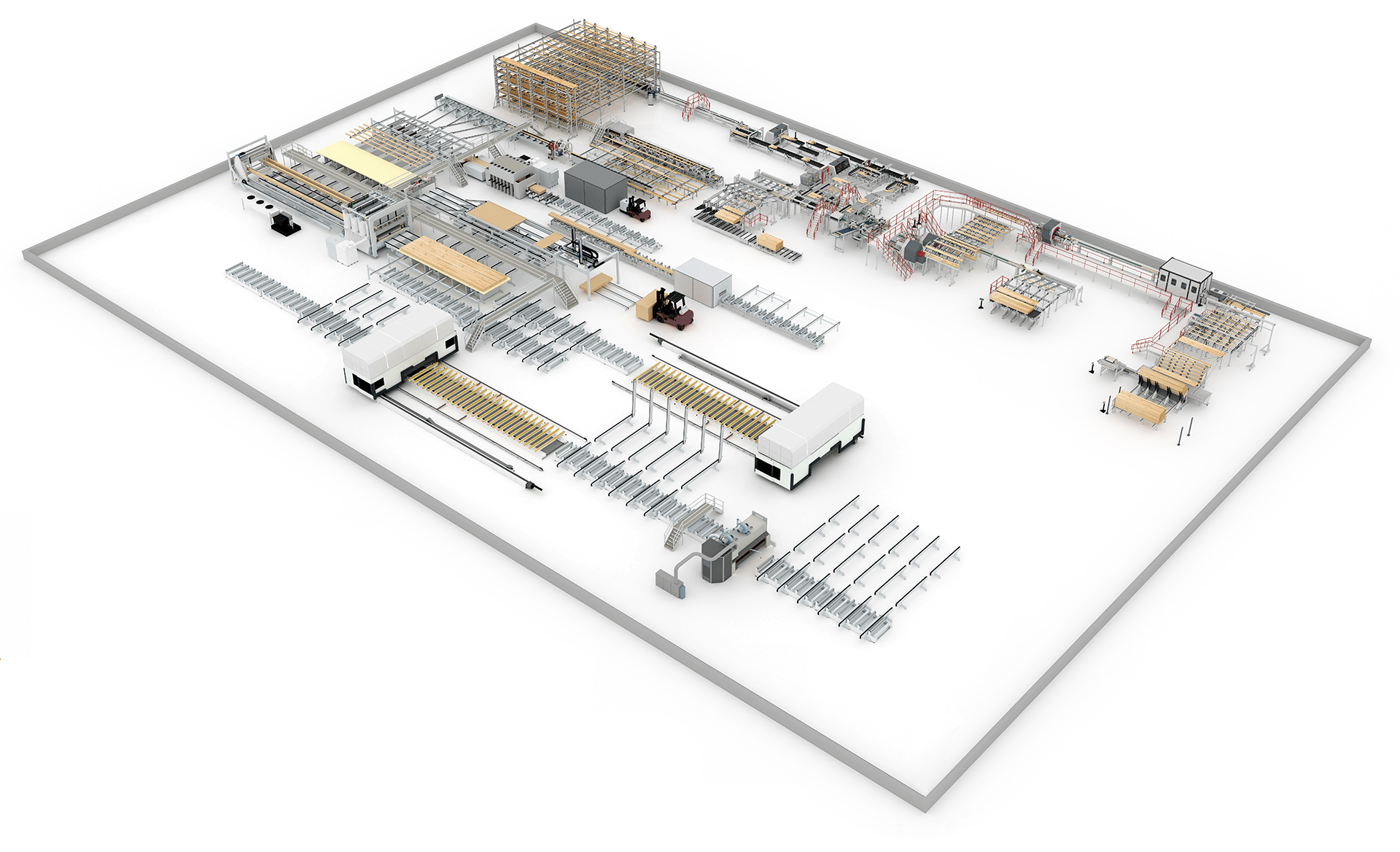
Glulam and CLT facility
Our most advanced system that offers you a compact flexible production line for glulam and CLT in one; from wood to engineered products.
Wood infeed includes complete grading system and finger jointing line with curing racks that serve as common delivery system for both production lines.
For CLT products where a fully closed surface is required, edge gluing can be included.
Both lines include our high frequency presses, that offer highest product quality and efficiency.
Optionally processing machines can be added on to complete a fully equipped facility.
Every machine part in the system is controlled by a fully automated computer system.
As an option the control system can be integrated into our advanced KMS Track&View software.
This software continuously keeps tracking the lamstock through the entire system, from infeed to finished product. Full control is obtained.
Combined system for glulam and CLT
Construction with CLT usually also requires the use of glulam beams, and this compact combination line can manufacture both products.
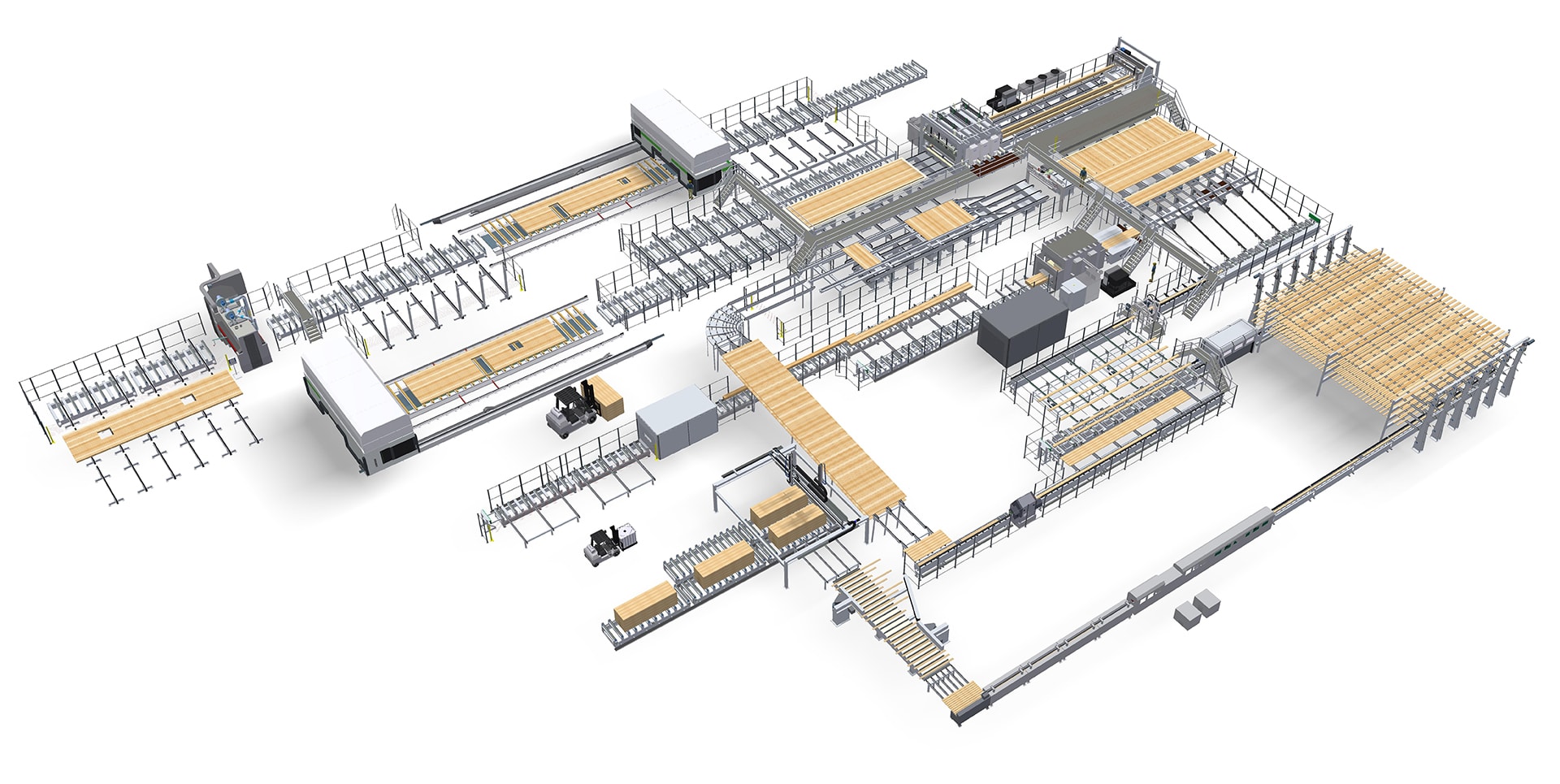
Combined system for glulam and CLT
Construction with CLT usually also requires the use of glulam beams, and this compact combination line can manufacture both products.
The two lines each require their own press and lay-up system for CLT and glulam beam production, respectively, but to optimize the production area, they use the same finger-jointing system, high storage, and mechanization.
Product specifications
CLT
Length: 4.000 – 20.000 mm
Width: 2.200 – 3.500 mm
Thickness: 60 – 400 mm
Beams
Length: 3.000 – 20.000 mm
Width: 860 – 1.250 mm
Thickness: 60 – 290 mm
Capacity (7,5 hours)
CLT
40 – 75 m3
Glulam
60 – 180 m3
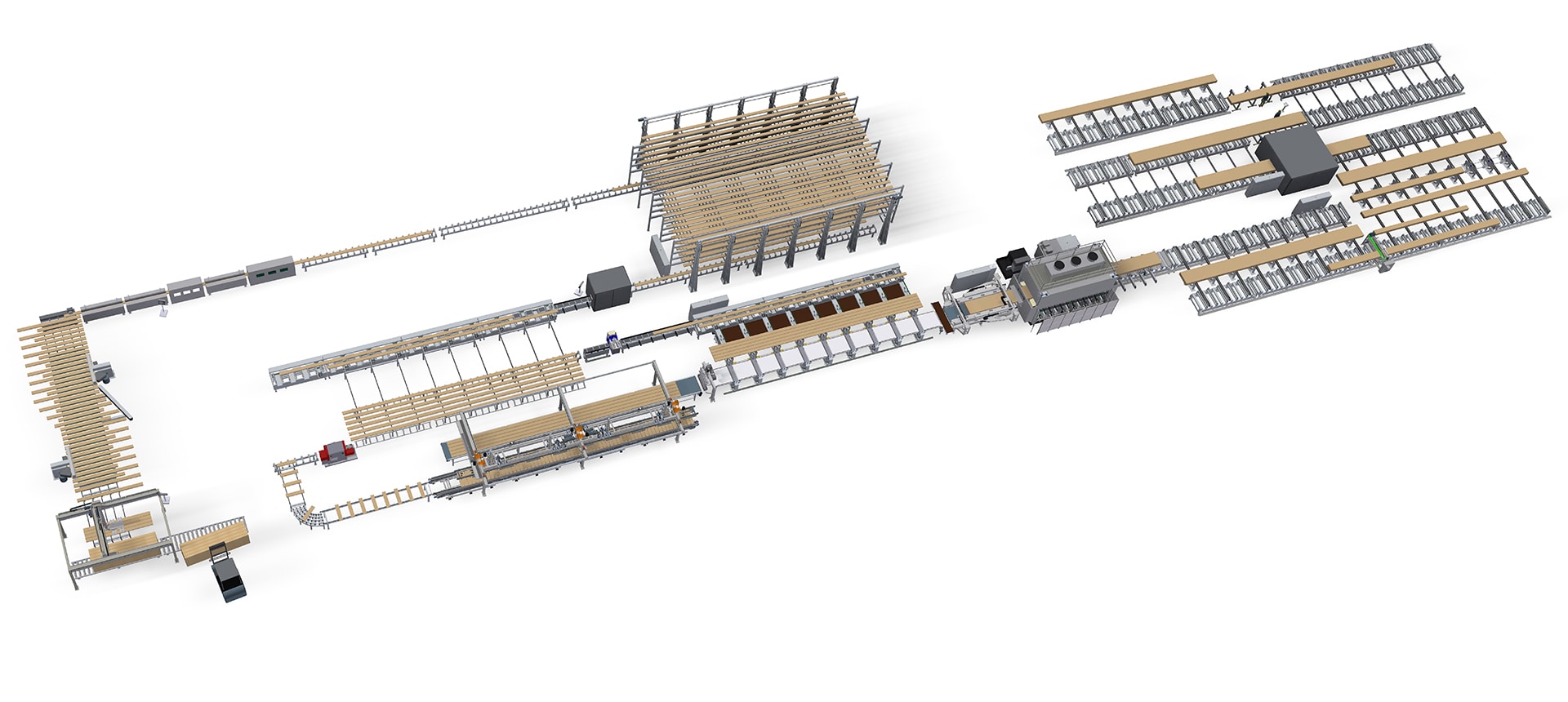
Press system for Glulam and CLT
With this combi solution you can produce Glulam and CLT in the same press line.
The complete line includes everything from finger jointing to delivery of finished elements.
After planing, lamellas from the high storage are brought to a position where they are packed either as beams or as the longitudinal layer of the CLT element. Alternatively, the lamstock can be passed from the high storage to a sawing line, which cuts the lamstock to a length to suit the cross-layer of the CLT element.
The long lamstock can be surface glued for beams or edge glued for the outer layer of the CLT element.
The lay-up system handles both beam lamstock, which is turned 90º, and CLT longitudinal lamstock, which is packed flat to form a layer.
CLT crosswise lamstock is added with a vacuum gantry.
After radio frequency pressing, the parts are transported for further processing and finishing.
Product specifications
Glulam
Length: 3.000 – 27.000 mm
Width: 260 – 1.250 mm
Heigth: 60 – 290 mm
CLT
Length: 6.000 – 20.000 mm
Width: 1.150 – 1.250 mm
Heigth: 60 – 290 mm
Capacity (7,5 hours)
Glulam
60 – 180 m3
CLT
30 – 50 m3
„Kallesoe were the only plant suppliers who kept what they had promised. Set up, turn on, produce“
„The line runs as it should – smoothly. The performance lives up to what was promised. We would buy the same machine all over again.“
“The Danes were really well prepared, and when it comes to machinery they are one of our most competent partners.”
“One of the reasons we went with Kallesoe Machinery is because they have been so accurate in their timelines, they do quality work, precision work and their ability to deliver a high-end product is something we feel very confident in”
“Kallesoe took the necessary time and adapted the machines to our individual needs.”
“Kallesoe has delivered as promised and supported us in the best possible way”
“We again opted for solutions by Kallesoe because of the high flexibility”
Contact
Let us find the right solution for you
References in the glulam industry
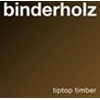
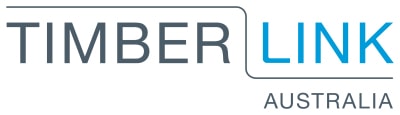
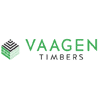
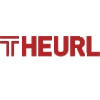
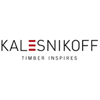
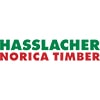
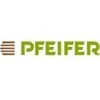
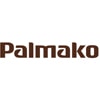
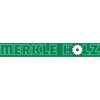
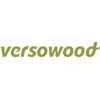
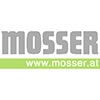
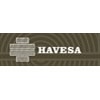
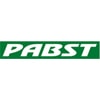
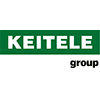
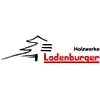
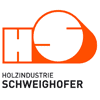
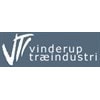
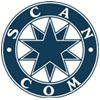
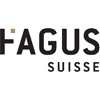
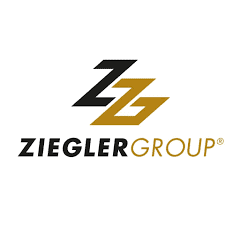