Custom-made solutions for high capacity CLT production
We know that it is crucial, you have exactly the right set-up for your CLT production. With decades of experience behind us and in close dialogue with you, we put together the right system solution for you and your business. This way you are guaranteed the highest quality and capacity with our state-of-the-art technology and flexible machine solutions.
We offer our expertise in custom-made, high-tech machinery for your CLT production that fulfills your site-specific production needs.
You know the need, together we find the solution.
Inspiration
Complete Factory Solution for CLT Production
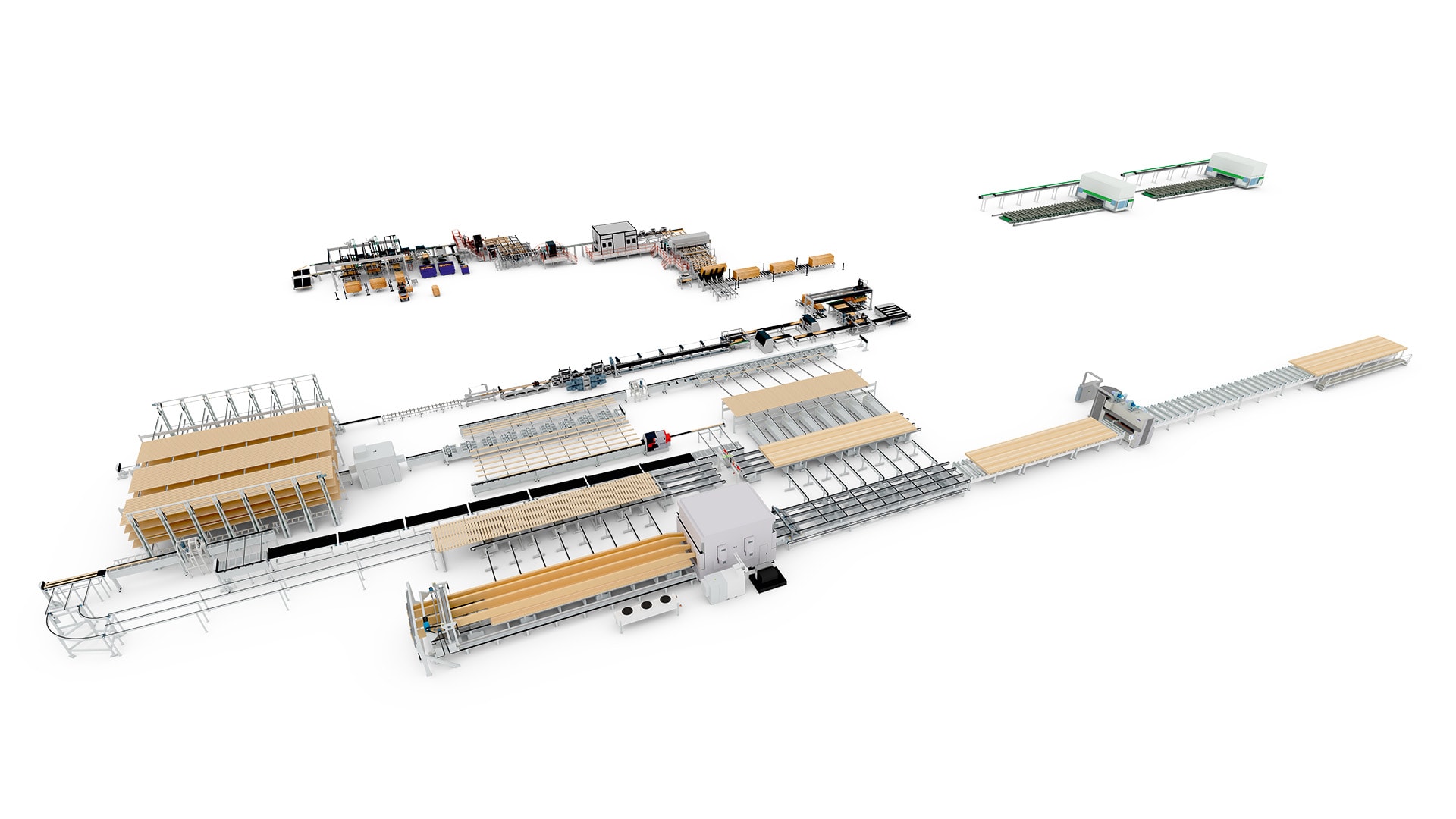
Basic CLT Line
A simple but very effective line for production of CLT.
The line consists of a grading and finger jointing system and high storage curing decks, followed by a lay-up system for transverse and longitudinal lamellas. Before entering the radio frequency CLT press, glue is applied between the layers.
Product Specifications
Length: 4.000 – 16.000 mm (13 – 53 ft)
Width: 2.200 – 3.200 mm (7,2 – 10½ ft)
Thickness: 60 – 400 mm (2,4 – 16 in)
Capacity
[7,5 hours] 60 – 80 m³
[7,5 hours] 2.100 – 2.800 ft³
A Compact CLT Facility
This production line is built around three separate presses.
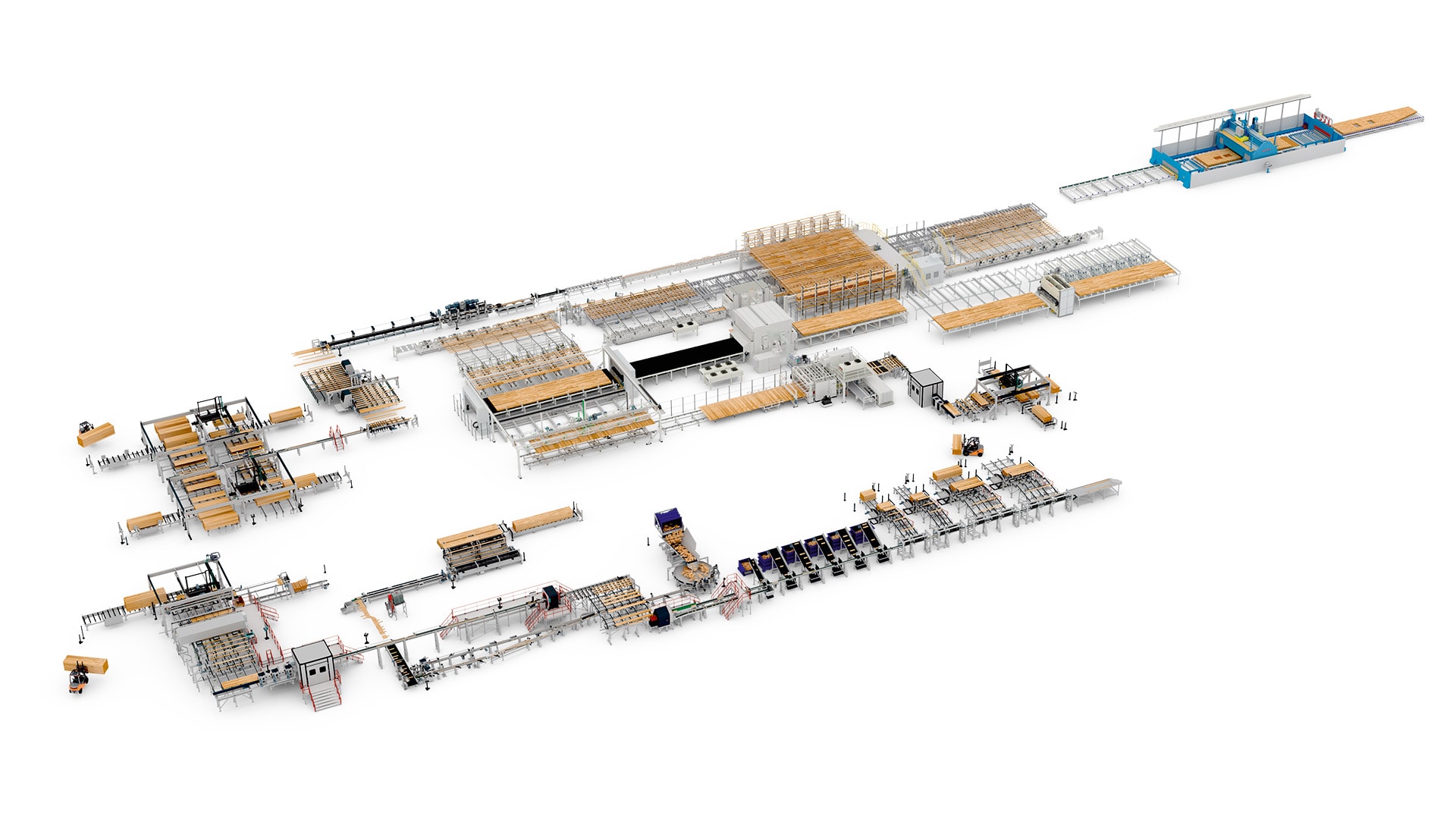
A Compact CLT Facility
This production line is built around three separate presses.
The first is for gluing transverse lamellas, the second for gluing of longitudinal lamellas, and lastly a solid CLT press for the final pressing of all the layers. All three presses use radio frequency to ensure fast curing of the glue. All in all, you get a fully glued CLT panel with this compact and high-standard solution.
Product Specifications
Length: 8.000 – 16.000 mm (26 – 53 ft)
Width: 2.200 – 3.500 mm (7,2 – 11½ ft)
Thickness: 51 – 400 mm (2 – 16 in)
Capacity
[7,5 hours] 60 – 80 m³
[7,5 hours] 2.100 – 2.800 ft³
High Capacity CLT Production Solution
This CLT solution has a very high capacity due to its two parallel presses.
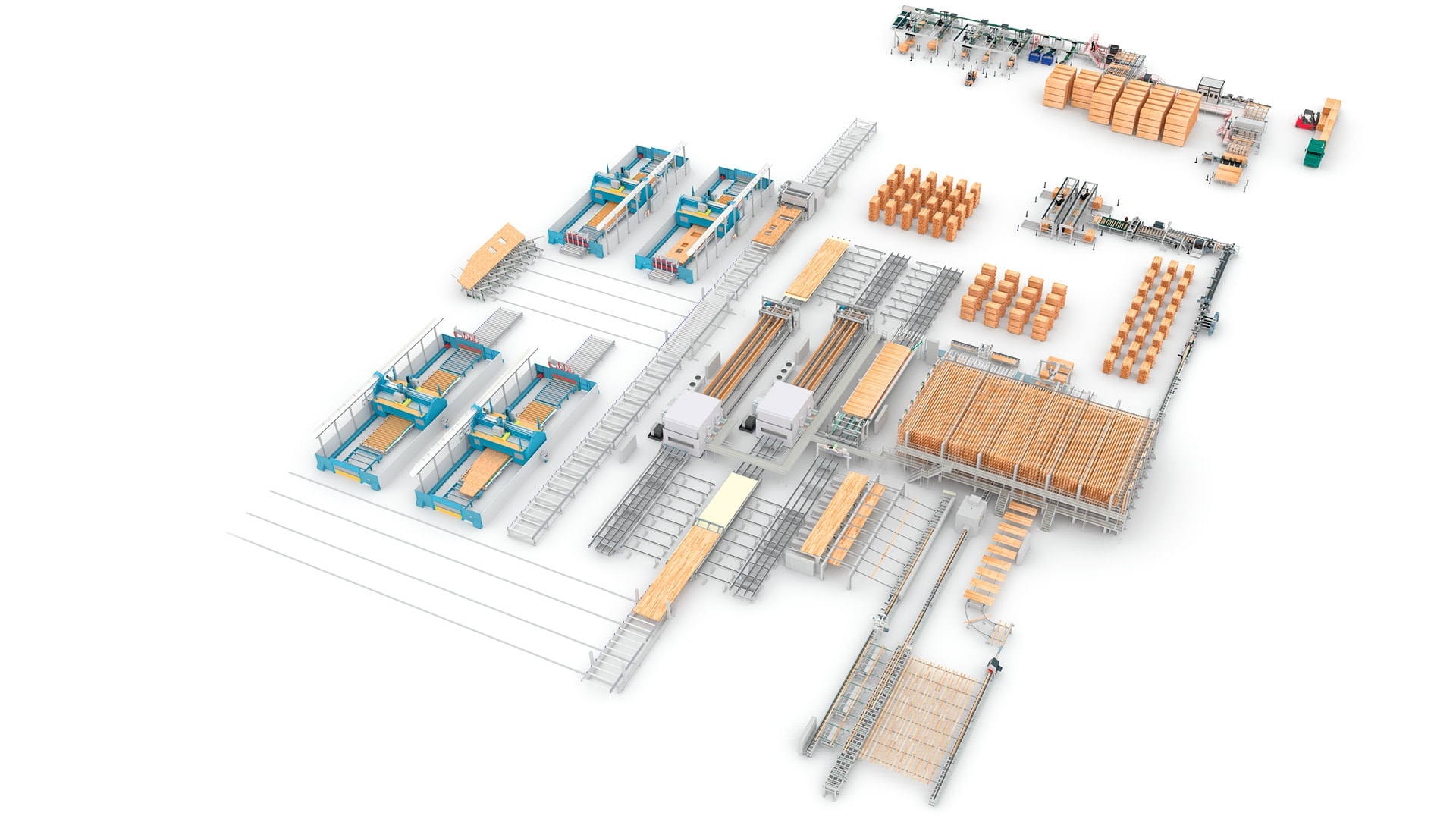
High Capacity CLT Production Solution
This CLT solution has a very high capacity due to its two parallel presses.
The two radio frequency presses are placed side by side, where they use the same grading, finger jointing, and lay-up system. This ensures full utilization of the machine capacity. After the pressing sequence, the CLT panels enter the CNC processing area.
Product Specifications
Length: 4.000 – 16.000 mm (13 – 53 ft)
Width: 2.500 – 3.500 mm (8,2 – 11½ ft)
Thickness: 60 – 400 mm (2,4 – 16 in)
Capacity
[7,5 hours] 120 – 160 m³
[7,5 hours] 4.200 – 5.600 ft³
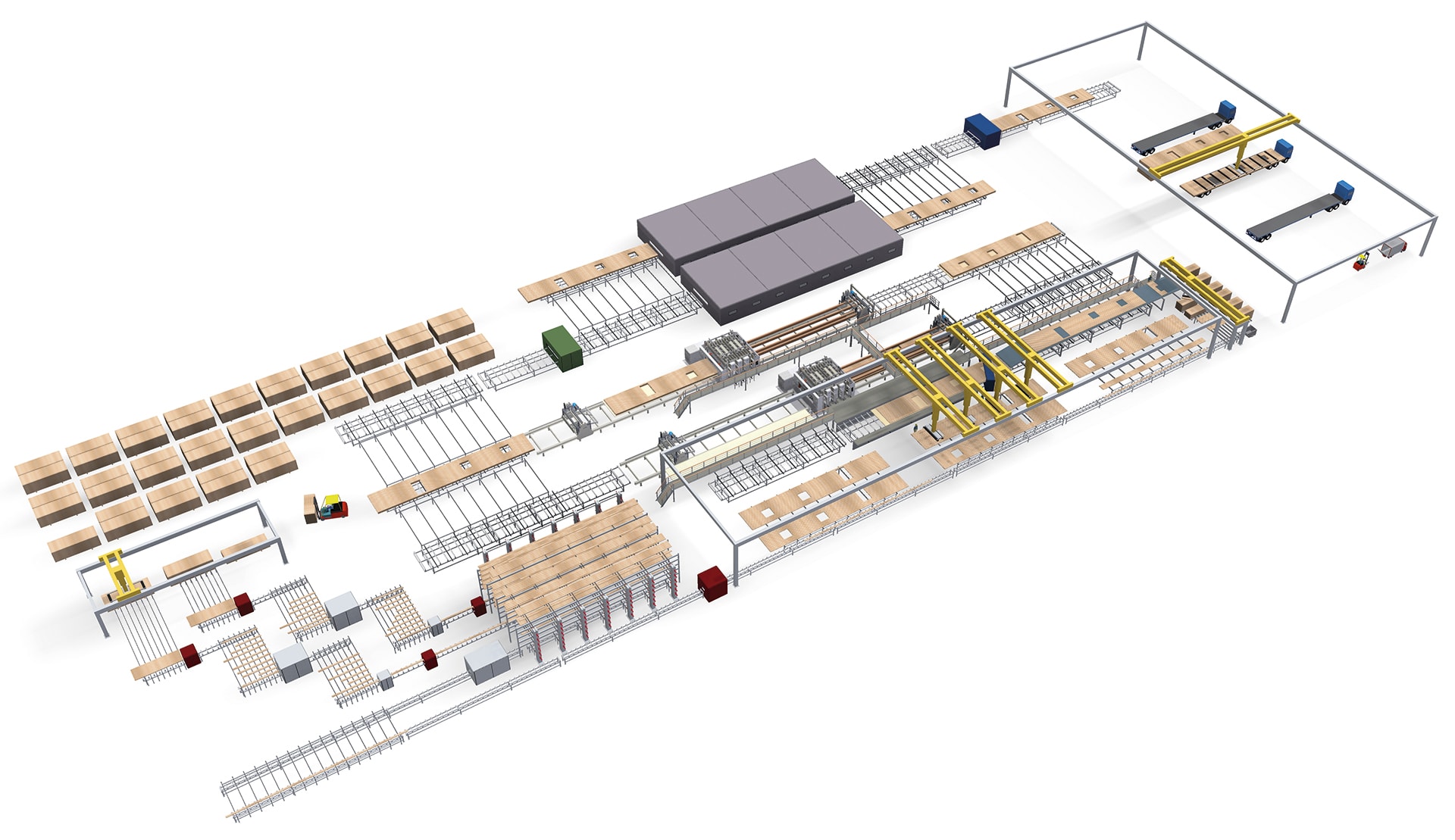
Complete CLT Manufacturing System
Fully equipped facility including feedstock infeed, finger jointing with curing area, lamstock layup with gluing, double press lines and CNC processing area.
The system uses vacuum for layup allowing openings to be prepared in the CLT panel such as door- and window openings. Thereby wood can be saved that would otherwise be wasted. The presses are fully integrated electronically and will cut off pressing cylinders in panel areas with openings.
Every machine part in the system is controlled by a fully automated computer system.
As an option the control system can be integrated into our advanced KMS Track&View software.
This software continuously keeps tracking the lamstock through the entire system, from infeed to finished product. Full control is obtained.
Product specifications
Length: 4.000 – 20.000 mm (14 – 65 ft)
Width: 2.200 – 3.500 mm (7 – 11.5 ft)
Thickness: 60 – 400 mm (2.4 – 15 in)
Capacity (7,5 hours)
130 – 160 m3
Joined CLT and Glulam Production Lines
This solution is ideal if you want to produce both CLT and Glulam.
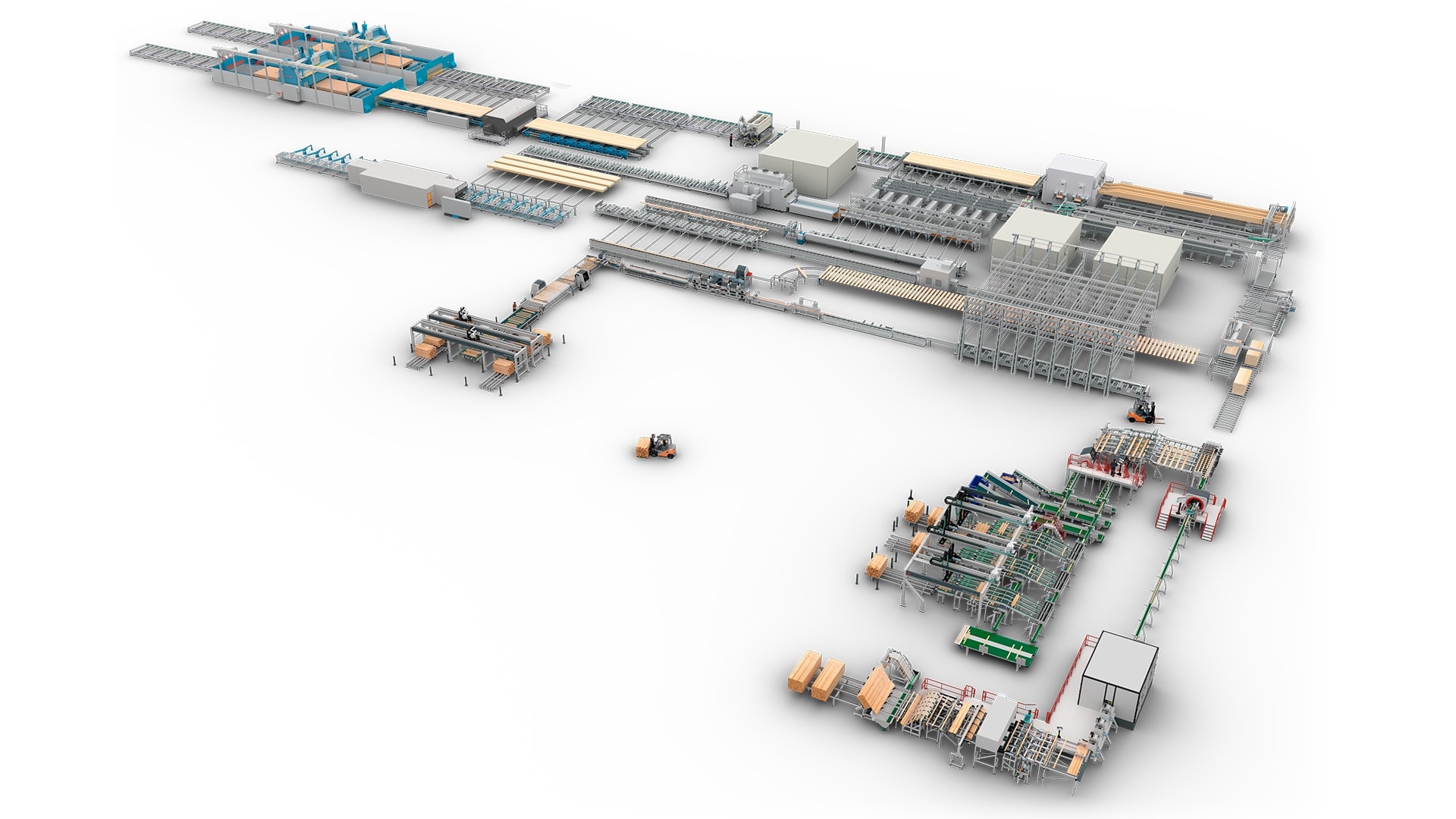
Joined CLT and Glulam Production Lines
This solution is ideal if you want to produce both CLT and Glulam.
With finger jointing serving both lines, this solution is both costs beneficial and time reducing. The CLT system can edge glue panels on both longitudinal and transverse layers. This offers a 100% edge and face glued CLT panel.
Product Specifications
CLT
Length: 6.000 – 18.000 mm (20 – 60 ft)
Width: 2.500 – 3.500 mm (8,2 – 11½ ft)
Thickness: 60 – 400 mm (2,4 – 16 in)
Glulam
Length: 6.000 – 18.000 mm (20 – 60 ft)
Height: Max. 1.280 mm (4 ft)
Width: 60 – 290 mm (2,4 – 11,5 in)
Capacity
CLT
[7,5 hours] 60 – 80 m³
[7,5 hours] 2.100 – 2.800 ft³
Glulam
[7,5 hours] 60 – 180 m³
[7,5 hours] 2.100 – 6.300 ft³
Combined System for CLT and Glulam
Construction with CLT usually also requires the use of glulam beams, and this compact combination line can manufacture both products.
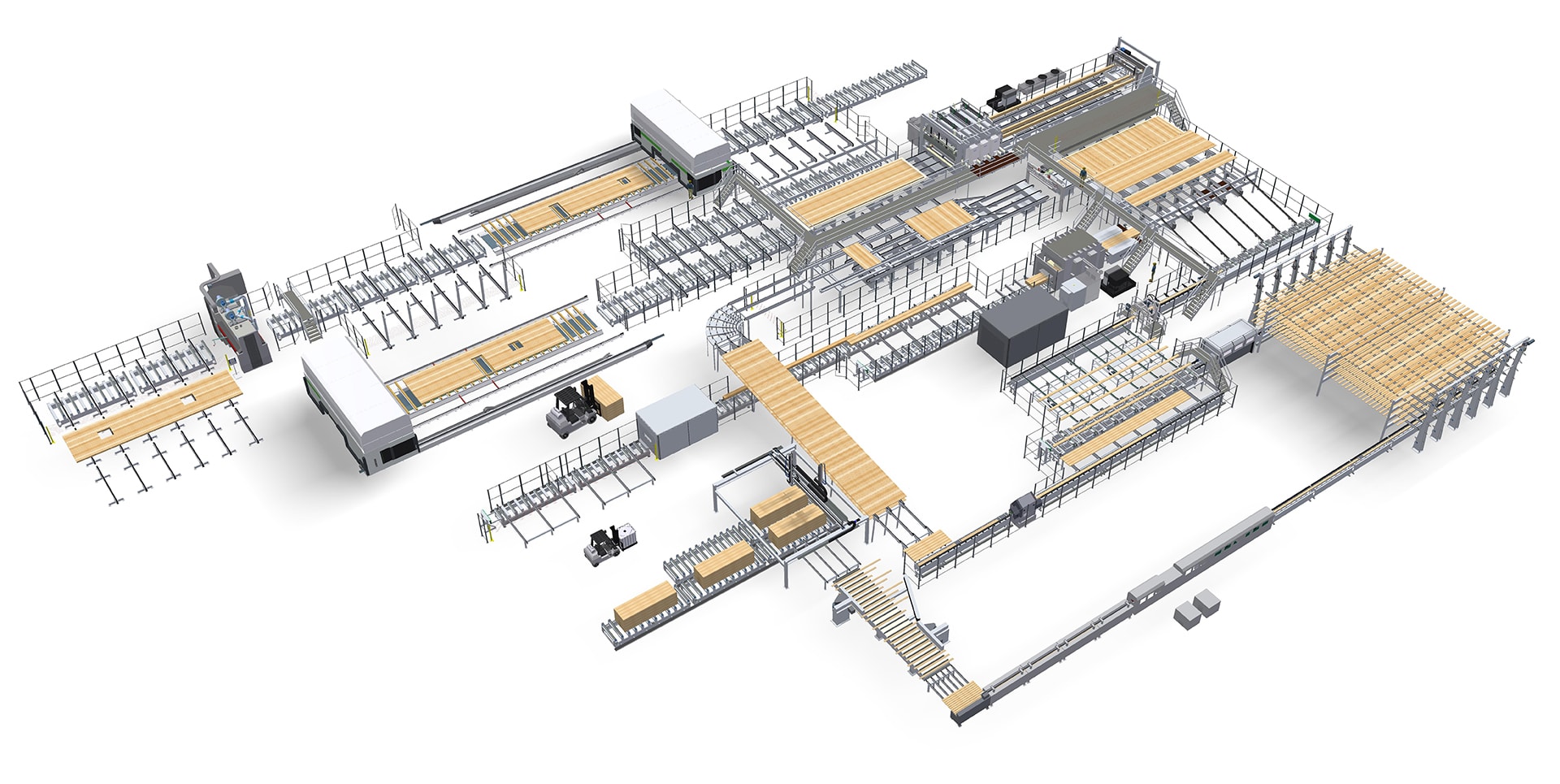
Combined System for CLT and Glulam
Construction with CLT usually also requires the use of glulam beams, and this compact combination line can manufacture both products.
The two lines each require their own press and lay-up system for CLT and glulam beam production, respectively, but to optimize the production area, they use the same finger-jointing system, high storage, and mechanization.
Product specifications
CLT
Length: 4.000 – 20.000 mm
Width: 2.200 – 3.500 mm
Thickness: 60 – 400 mm
Glulam
Length: 3.000 – 20.000 mm
Width: 860 – 1.250 mm
Thickness: 60 – 290 mm
Capacity (7,5 hours)
CLT
40 – 75 m3
Glulam
60 – 180 m3
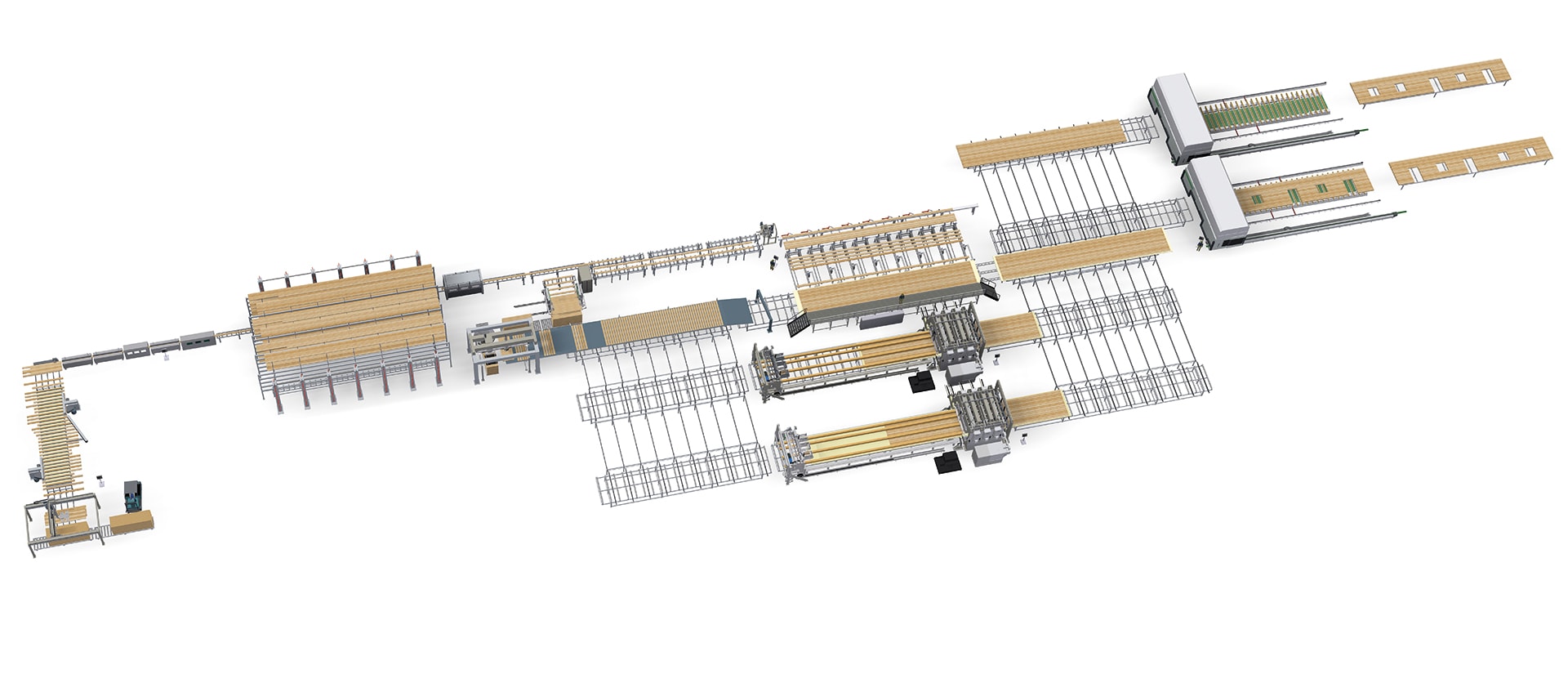
CLT System Prepared for Extension
This CLT press line is a flexible solution with an option to add more presses into the same production line.
The solution gives you the option to start with a smaller investment and scale up as you need it.
Both presses use the same finger jointing, high storage, and lay-up system.
Crosswise lamstock is added as ready cut lamstock, or the function can be integrated into the line.
It is possible to design the production line with required machining centers.
Product specification
Length: 4.000 – 20.000 mm
Width: 2.200 – 3.500 mm
Thickness: 60 – 400 mm
Capacity (7,5 hours)
130 – 160 m3
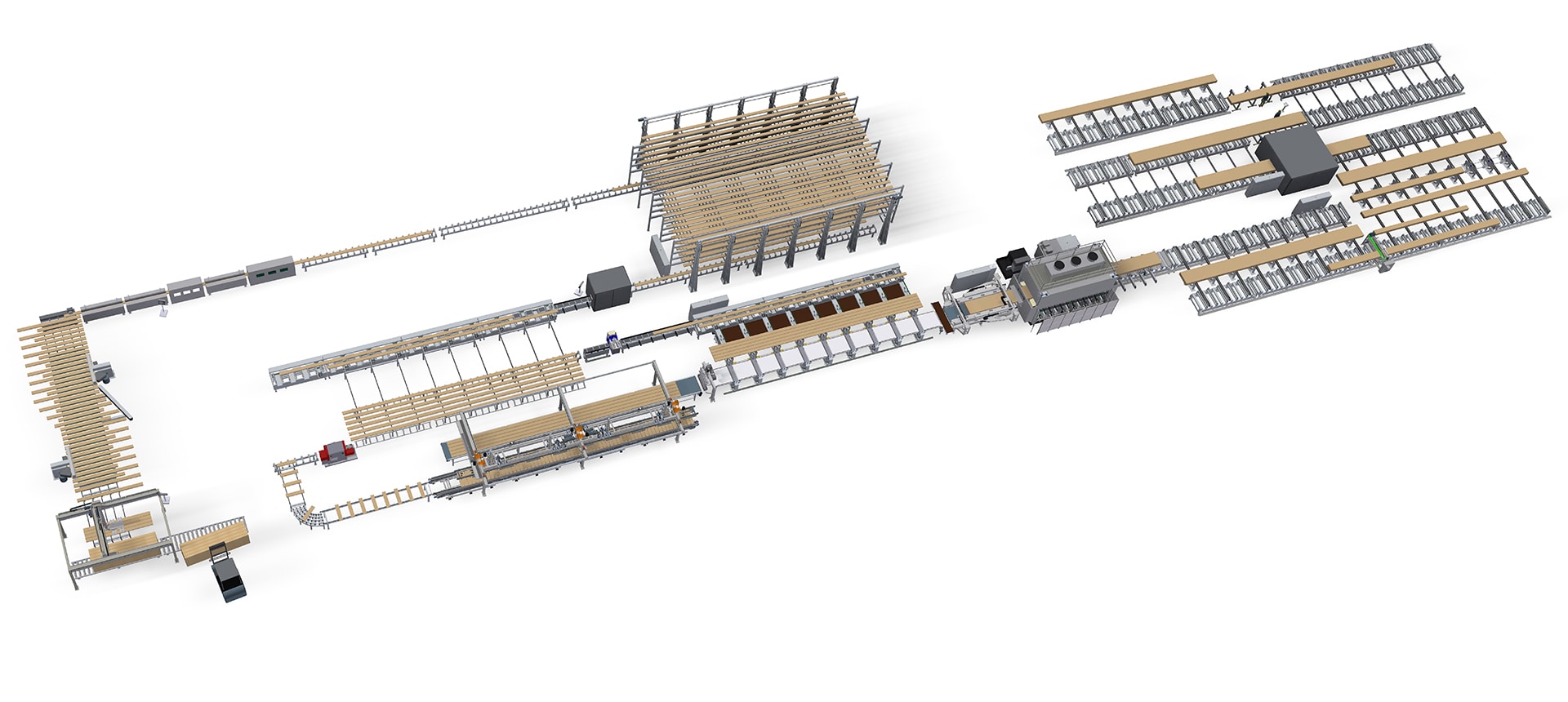
Combi Press System for CLT and Glulam
With this combi solution you can produce CLT and glulam in the same press line.
The complete line includes everything from finger jointing to delivery of finished elements.
After planing, lamellas from the high storage are brought to a position where they are packed either as beams or as the longitudinal layer of the CLT element. Alternatively, the lamstock can be passed from the high storage to a sawing line, which cuts the lamstock to a length to suit the cross-layer of the CLT element.
The long lamstock can be surface glued for beams or edge glued for the outer layer of the CLT element.
The lay-up system handles both beam lamstock, which is turned 90º, and CLT longitudinal lamstock, which is packed flat to form a layer.
CLT crosswise lamstock is added with a vacuum gantry.
After radio frequency pressing, the parts are transported for further processing and finishing.
Product specification
CLT
Lenght: 6.000 – 20.000 mm
Width: 1.150 – 1.250 mm
Thickness: 60 – 290 mm
Glulam
Length: 3.000 – 27.000 mm
Width: 260 – 1.250 mm
Thickness: 60 – 290 mm
Capacity (7,5 hours)
CLT
30 – 50 m3
Glulam
60 – 180 m3
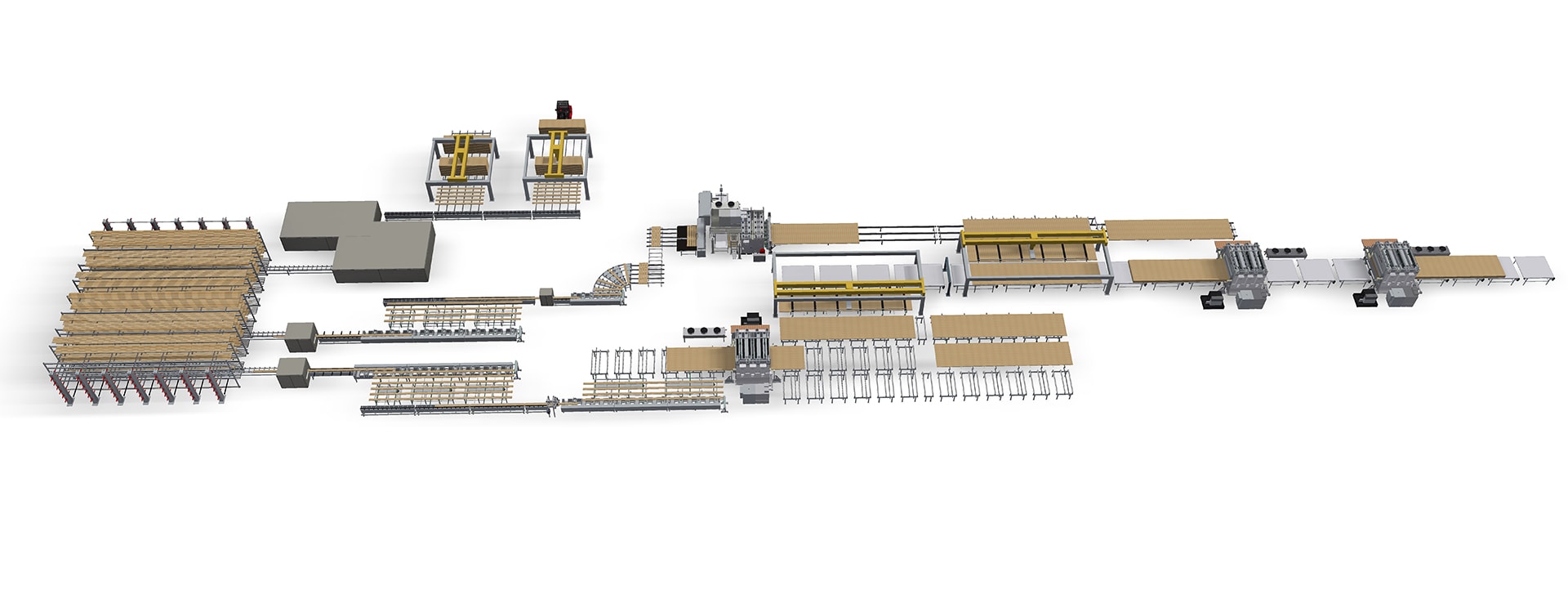
CLT Solution with Edge Gluing of the Lamstock
With this CLT press line you can glue the edge of the crosswise and lengthwise lamstock.
In this CLT production line, the individual lamella layers can be glued together, and the glue be cured in separate presses before being stacked into a CLT-element.
Two vacuum cranes place finished layers of lengthwise and crosswise lamstock on top of each other. For each layer, the element is moved back and forth under the glue applicator until the desired number of layers is reached. The CLT-element is then transported to one or more presses for final curing of the glue.
Product specification
Length: 4.000 – 20.000 mm
Width: 2.200 – 3.500 mm
Thickness: 60 – 400 mm
Capacity (7,5 hours)
120 – 130 m3
CLT and Glulam Production System
Complete plant for the production of CLT and glulam beams using the same feeding system.
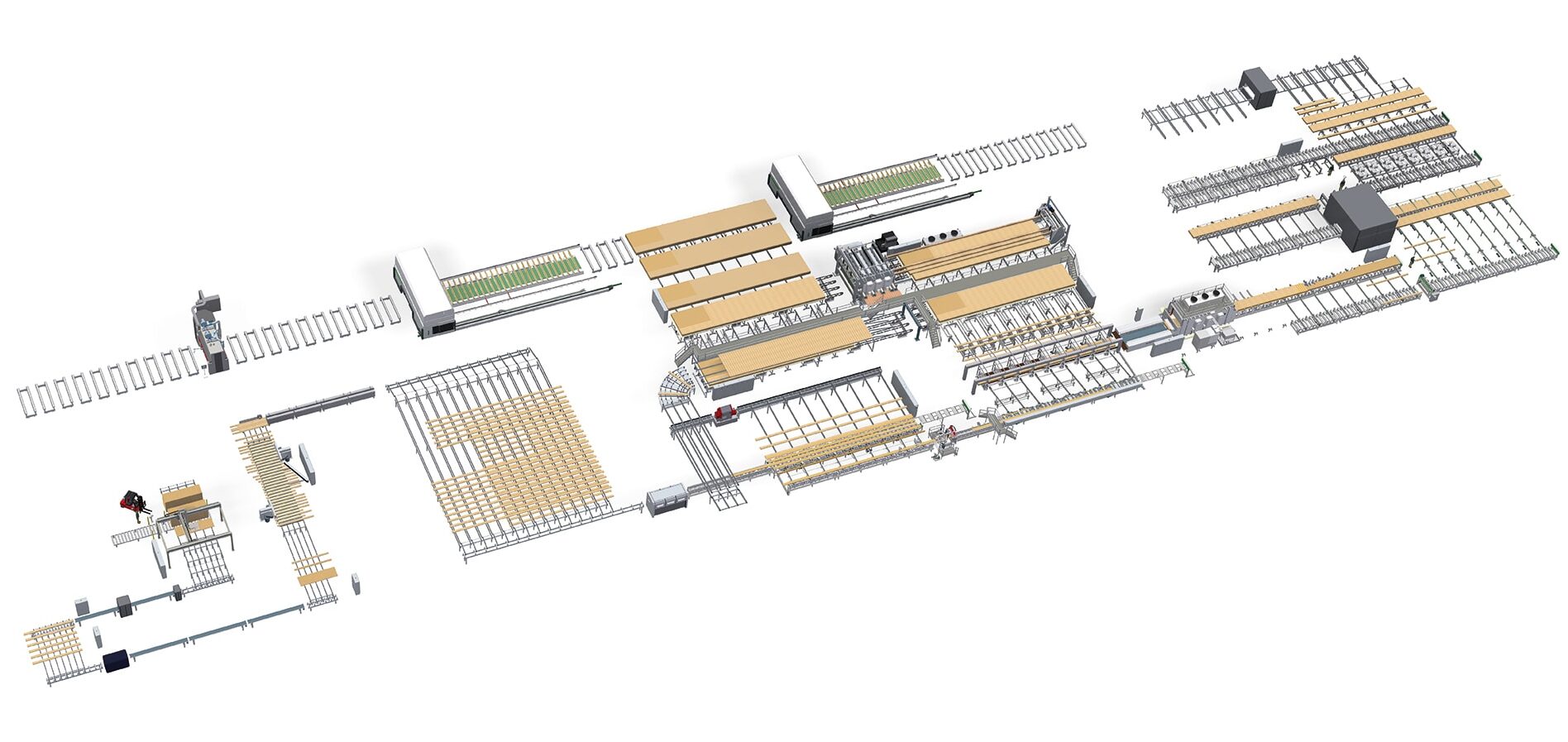
CLT and Glulam Production System
Complete plant for the production of CLT and glulam beams using the same feeding system.
In order to reduce the space requirement, this plant uses the same finger jointing and storage system for the production of both CLT and glulam.
The lamstock is then distributed to the two lines where it is used for glulam beams, for lengthwise CLT-layers and (after having been cut) for crosswise CLT-layers.
In this layout, both lines are equipped for finishing machinery: the beam line with a cross-cut saw, a planer, repair stations and wrapping equipment, the CLT-line with CNC machines and sanding machines.
Product specifications
CLT
Length: 4.000 – 20.000 mm
Width: 2.200 – 3.500 mm
Thickness: 60 – 400 mm
Glulam
Length: 3.000 – 20.000 mm
Width: 860 – 1.250 mm
Thickness: 60 – 290 mm
Capacity (7,5 hours)
CLT
40 – 75 m3
Glulam
60 – 180 m3
“We have been in this business for 82 years. Kallesoe is by far the best and most professional supplier we have ever done business with. They are so easy to work with, and they know their products and business area. It has been a pleasure. It is important to go the extra mile to make sure that the customer is satisfied – and they do that at Kallesoe.”
“Kallesoe took the necessary time and adapted the machines to our individual needs.”
”Kallesoe Machinery is state-of-the-art and absolutely market leader for this type of equipment, so we had to have these machines. They are the tomorrow’s system for the production of glulam beams”
„Kallesoe were the only plant suppliers who kept what they had promised. Set up, turn on, produce“
References in the CLT industry
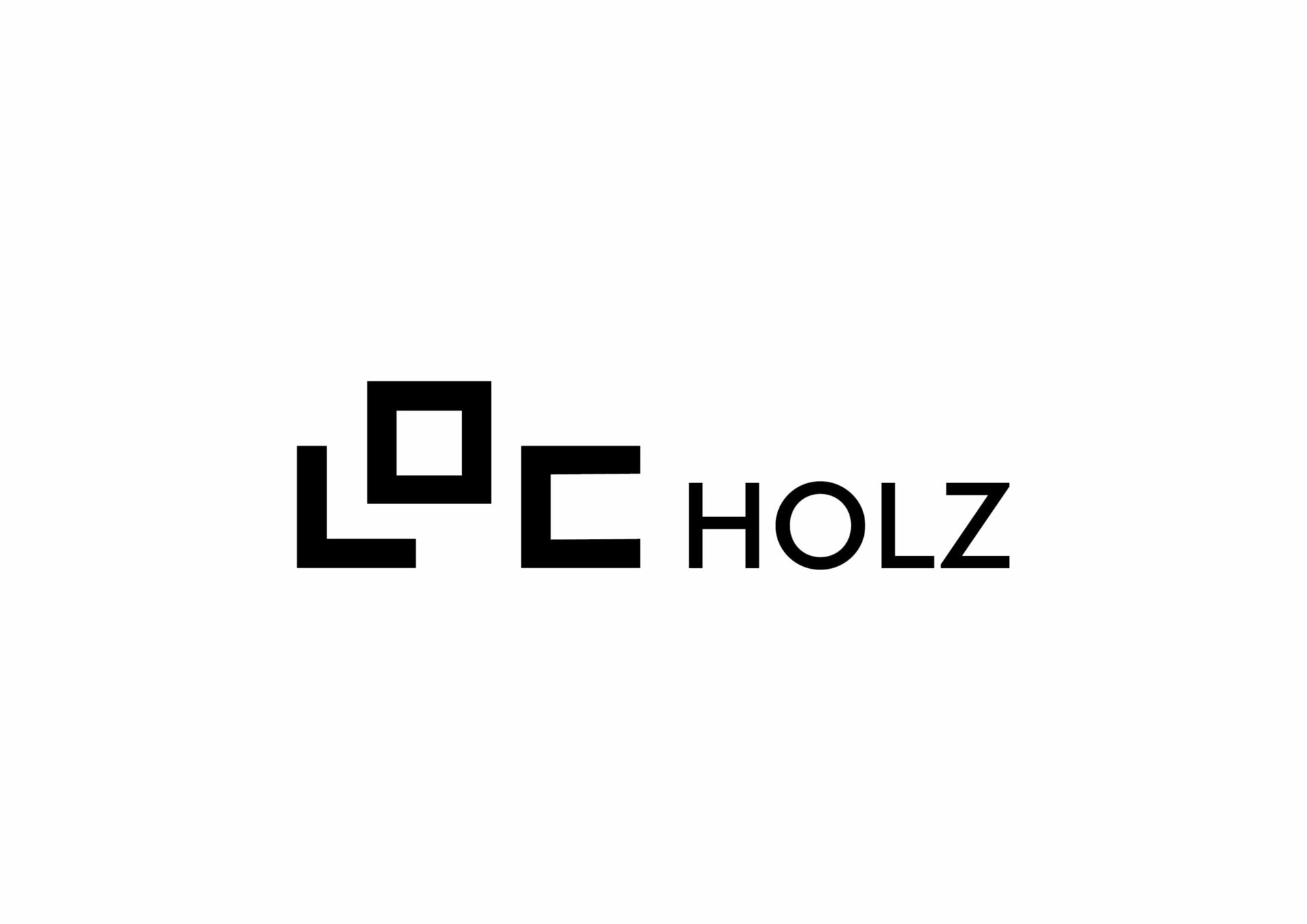
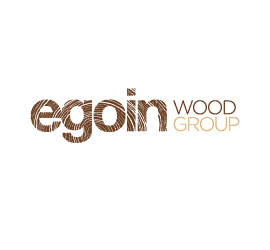
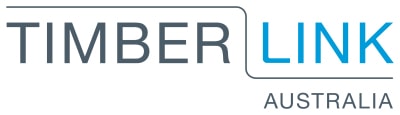
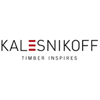
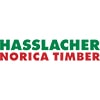
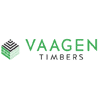
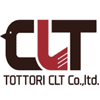
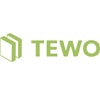
Download