Custom-made solutions for solid wood board production
We are dedicated to find the best system solution for your solid wood board production. In close collaboration with you we develop the right set-up for your production with our flexible machine solutions and latest technology. With our custom-made system solutions you can optimize your production, so you achieve the highest capacity in premium quality.
Our machinery can be adapted to your site-specific production needs. With our creative and innovative approach, we can guarantee you get an effective production of high quality.
Find examples of our board production here
Your solution is designed uniquely for you
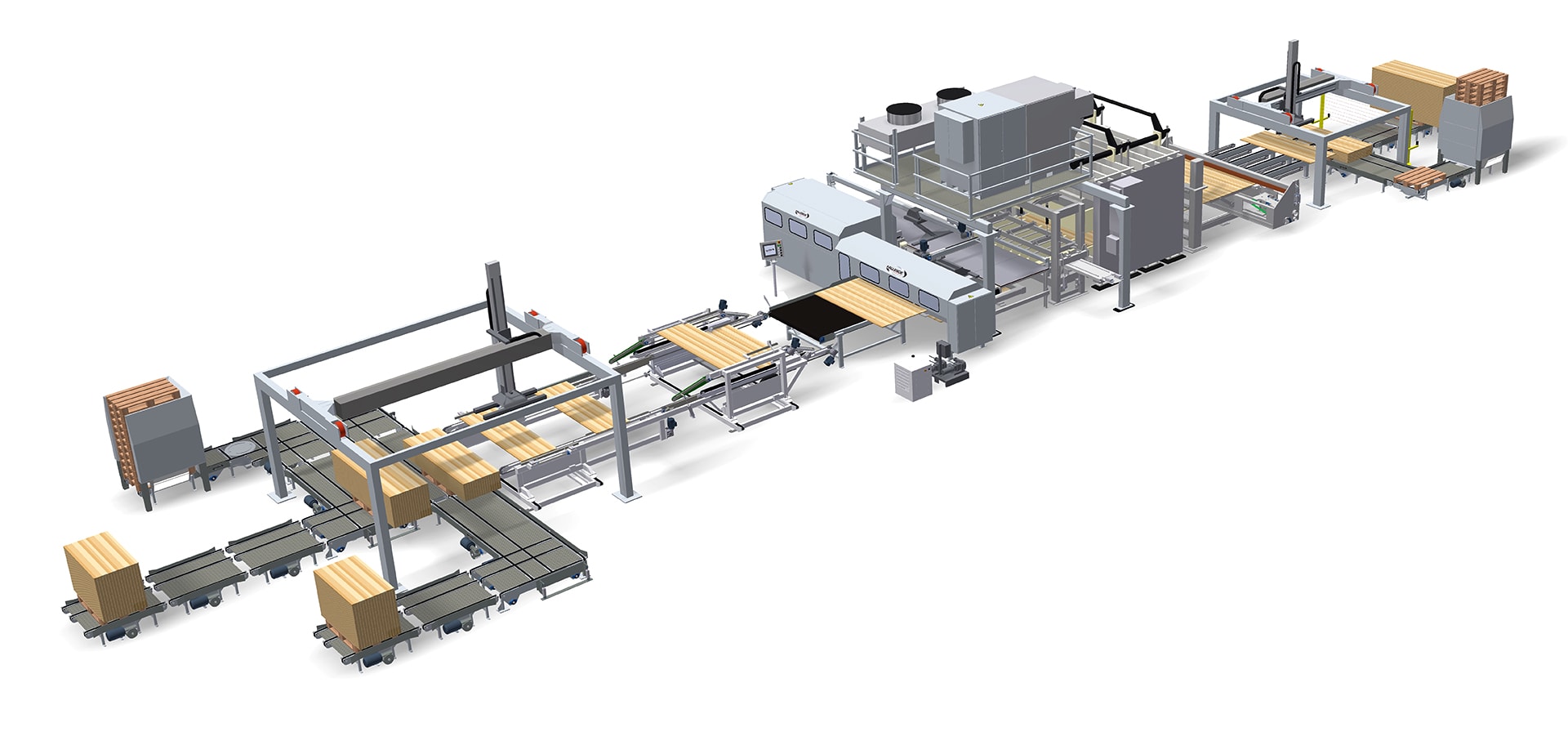
High speed board manufacturing system
For mass production of solid wood boards, we recommend our Q press system with radio frequency technology.
This solution has a sorting system that feeds the lamstock into the glue applicator in a systematic order depending on the desired quality of the boards. The Kallesoe edge glue applicator ensures an operation running optimally as well as the best use of the glue. The glue applicator can be set to skip pieces of lamstock if a separation of the boards is wanted.
After the glue applicator the lamstock is joined in a batch that is led in front of the press. A unit pushes the batch into the radio frequency field with the wanted laminating pressure, the radio frequency is activated, and the glue is heated from the inside and outwards.
From the HF field the batch is moved further to a hot water press, where the glue is cured from the outside and inwards. This ensures that the glue is completely hardened when it exits on the outlet side, and that the boards will not stick together when they are stacked with the vacuum stacker.
We offer a cross saw for placing between the press and stacker, that can shorten the boards to the desired dimensions.
Product specifications:
Length: ∞ mm/ft
Width: 1,000-6,100 mm (3 – 20 ft)
Thickness: 8-45 mm (0.3 – 1.8 in)
Capacity (7,5 hours)
1500 – 2500 m2
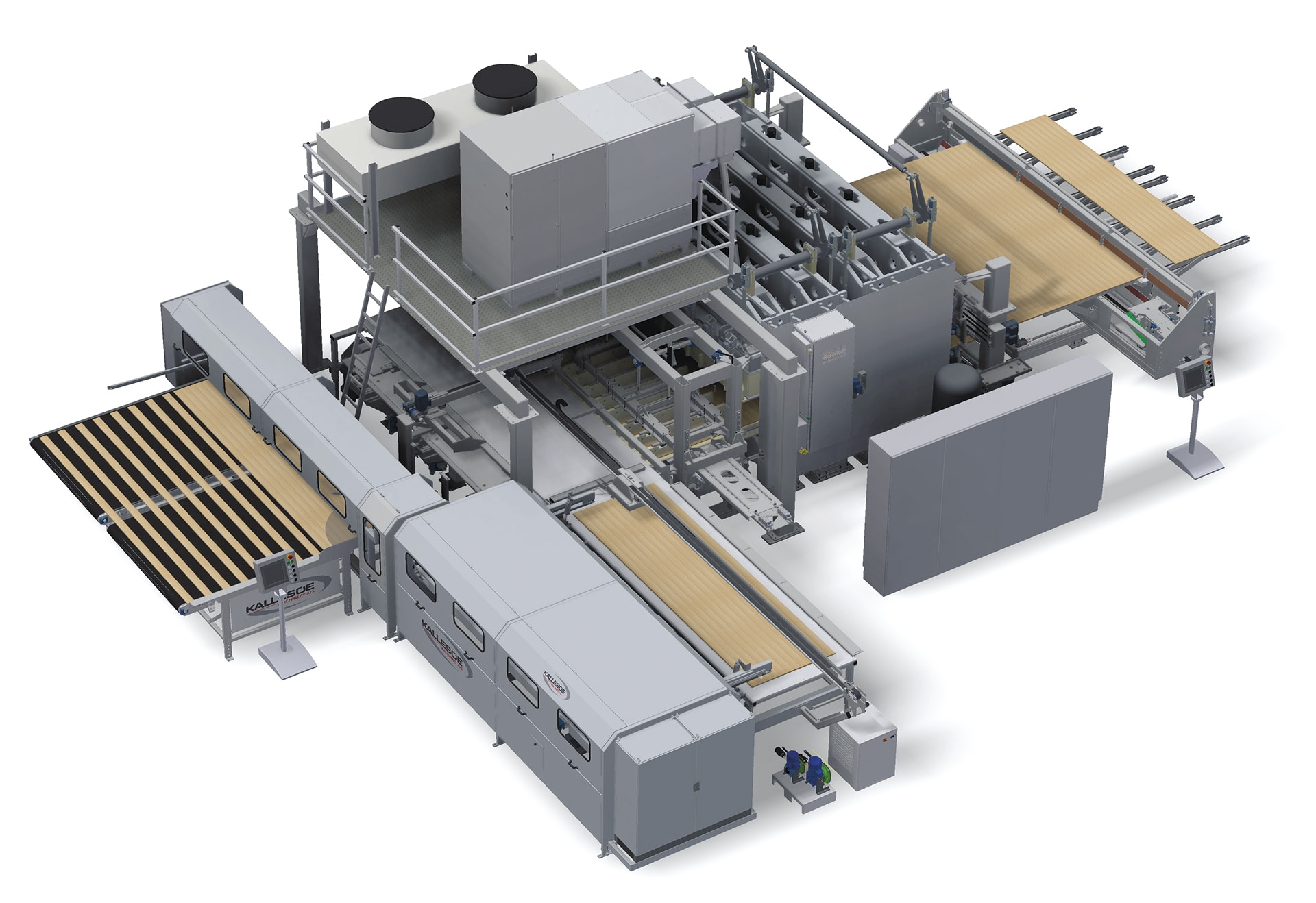
Press system for endless boards
The Q-press system is an extremely effective radio frequency press for board production.
This system solution uses radio frequency energy to cure the glue from the inside and out. From the HF field the batch is moved further to a hot water press, where the glue is cured from the outside and inwards. This ensures that the glue is completely hardened when it exits on the outlet side, and that the boards will not stick together when they subsequently are stacked with the vacuum stacker.
We offer a cross saw for placing between the press and stacker, that can shorten the boards to the desired dimensions.
Product specifications:
Length: ∞ mm/ft
Width: 1,000-6,100 mm (3 – 20 ft)
Thickness: 8-45 mm (0.3 – 1.8 in)
Capacity (7,5 hours)
1500 – 2500 m2
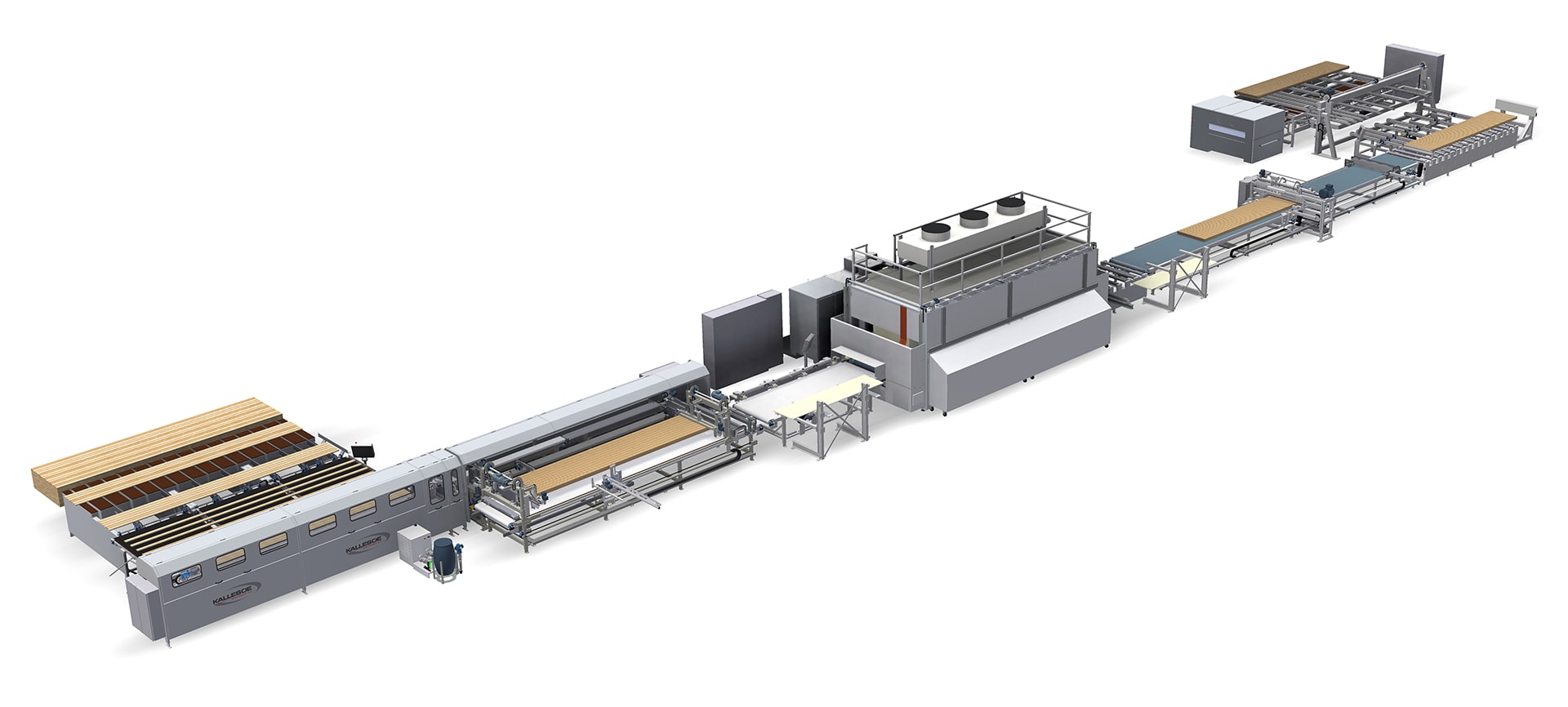
Press system for boards and small glulam
LHF press with radio frequency technology for production of solid wood boards and small beams.
This solution uses a standard LHF press with radio frequency technology to produce both small beams and solid wood boards. The glue system is type KL80 that is characterized by its ability to edge glue and face glue the lamstock depending on the type of product the press is manufacturing. When the lamstock are glued the are continuously gathered in a batch, and when the batch is full it is led into the press. The finished product can subsequently be sawed to the desired length and stacked.
Product specifications
Length: 1,000-6,000 mm (3.3 – 20 ft)
Width: 860-1,250 mm (2.8 – 4 ft)
Thickness: 15-150 mm (0.6 – 6 in)
Capacity (7,5 hours)
Boards:
40 – 120 m3
Glulam:
40 – 120 m3
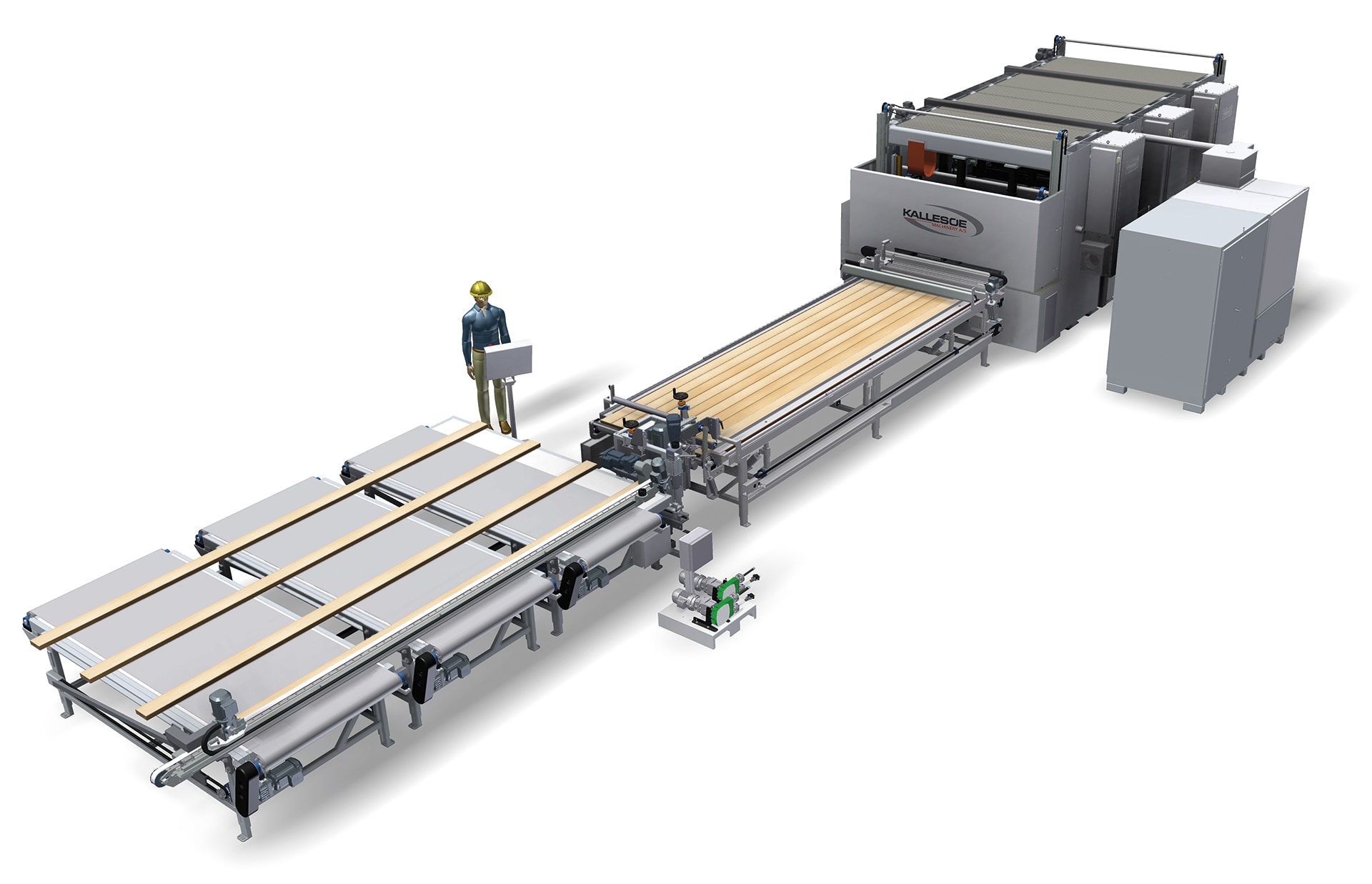
Press system for thick boards
The B-press system is specially designed for production of long and thick boards in high quality.
This system solution with the very stable and efficient KL 10 lay-up system is especially suitable for lay-up of lamstock with thicker and longer dimensions than typically used for furniture boards.
The equipment handles lamstock of up to 80 mm in thickness and the length of the lamstock will typically be 6 meters.
The lamstock are individually pushed through the edge glue applicator and there after they are laid-up in the desired width on the collection unit in front of the press.
The element is transported into the HF press which ensures the fastest curing of the glue.
After pressing the board can be sawed and stacked.
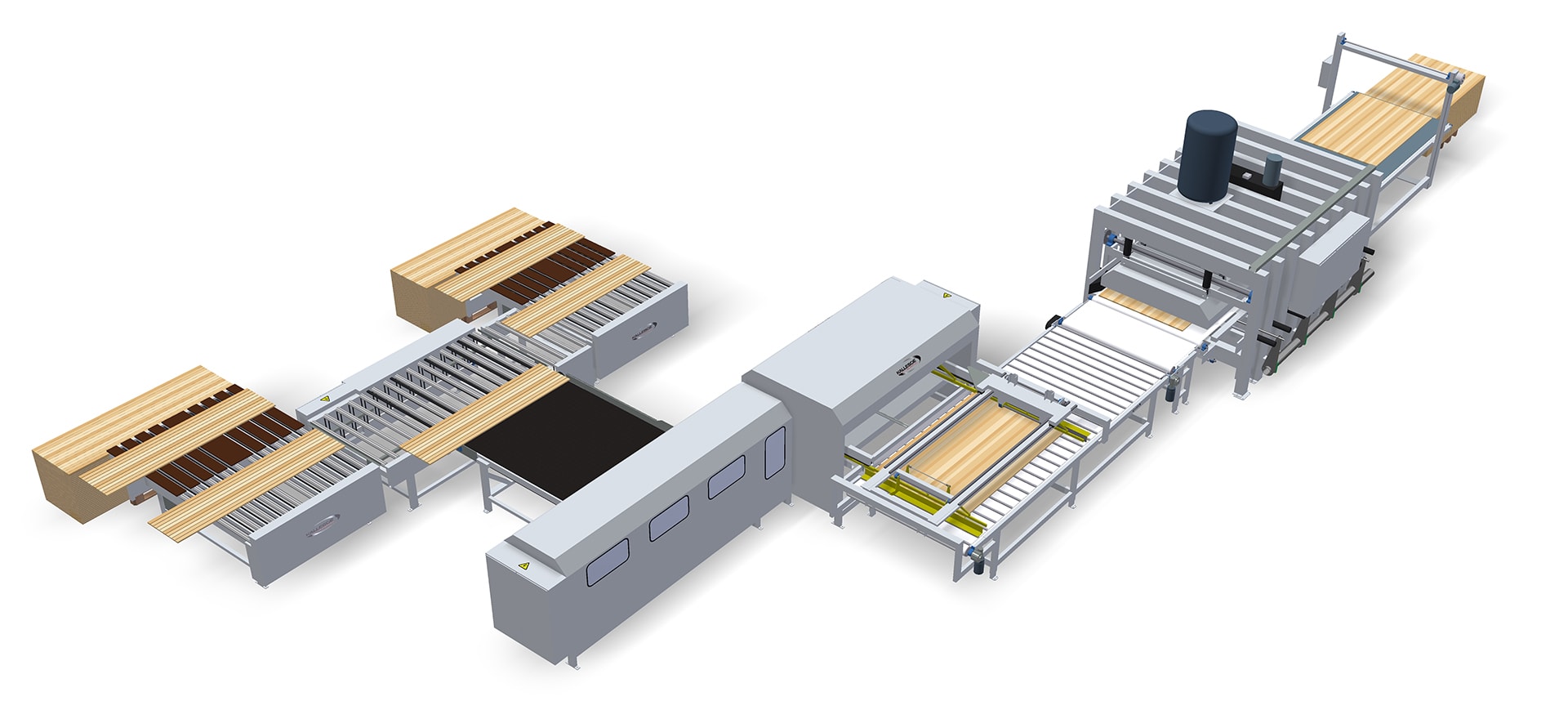
Press system for furniture boards
Cost effective solution for manufacturing boards and panels
The production line includes a manual double sorting system with infeed to the glue and lay-up system type KL 40.
The lay-up system operates with a speed up to 200 m/min. and is especially suitable for shorter lamella lengths up to 2.5 m.
A buffer zone allows for the next incoming charge to be placed, so a continuous flow can be maintained.
The full table batch is led to the hot-press that cures this type of thin products in the shortest amount of time.
Handling equipment after the press can be added e.g. a stacking unit.
„Kallesoe were the only plant suppliers who kept what they had promised. Set up, turn on, produce“
“One of the reasons we went with Kallesoe Machinery is because they have been so accurate in their timelines, they do quality work, precision work and their ability to deliver a high-end product is something we feel very confident in”
“The technology was very impressive. We are convinced that it is much better than other technologies on the market. It is all about flexibility and speed.”
“Kallesoe took the necessary time and adapted the machines to our individual needs.”
References in the solid wood board industry
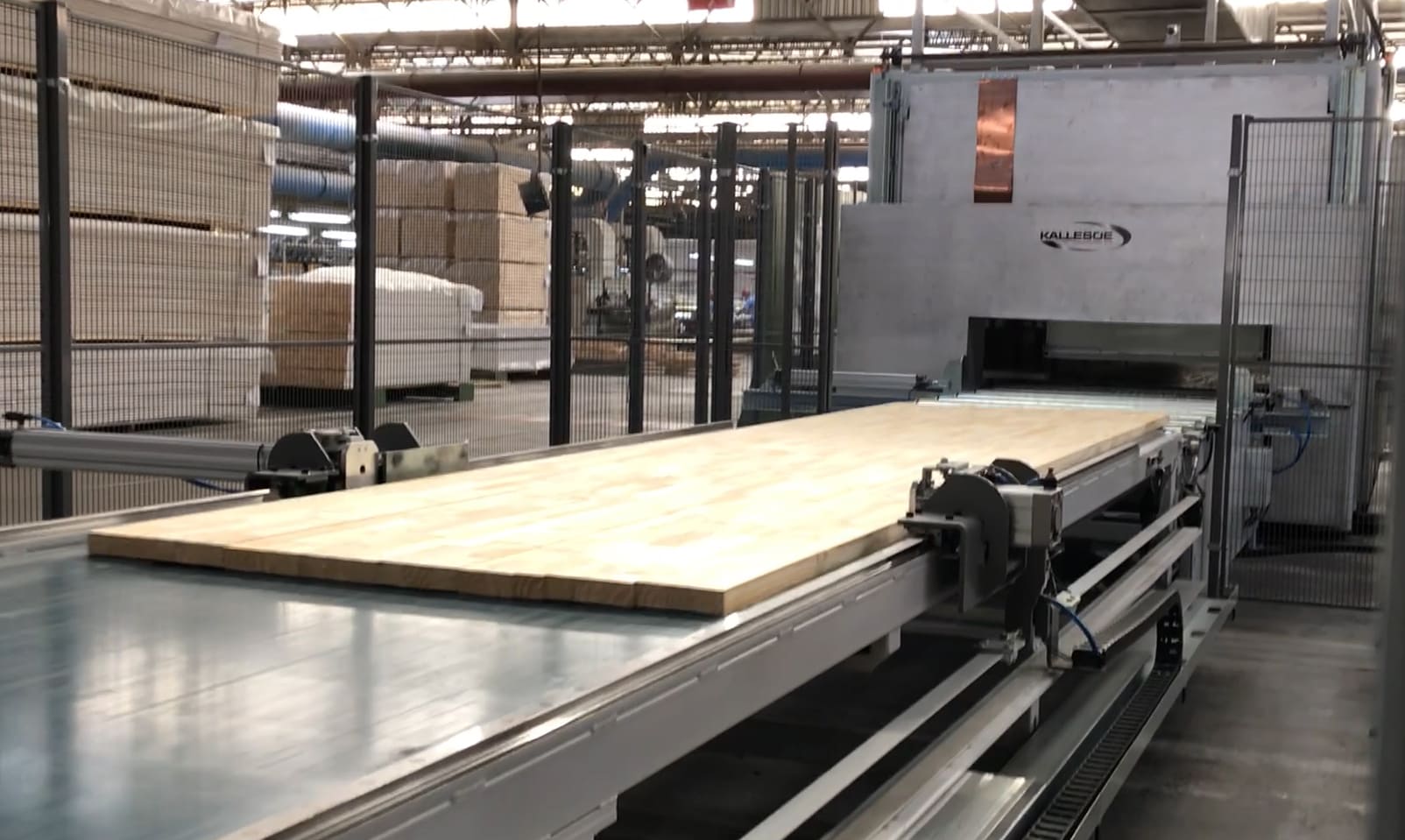
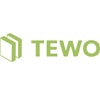
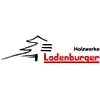
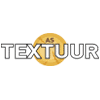
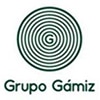
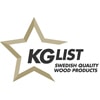
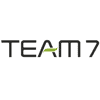
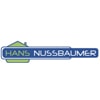
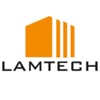
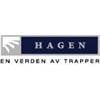
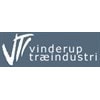
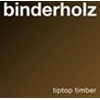